Pra nós, basta olhar pra um objeto e dizer que ele possui plástico, borracha, cerâmica e ou metal em sua composição, mas não é bem assim que as coisas funcionam.
Plástico não é “tudo igual”, assim como a borracha e o metal também não são. É comum as pessoas classificarem a qualidade de um produto de acordo com essas terminologias, porém devemos saber que há centenas de polímeros diferentes, que proporcionam milhares de combinações, isto é, compósitos, que permitem agregar qualidades de diferentes materiais e criar produtos de alta qualidade.
Mas para sabermos definir a qualidade de um produto, precisamos conhecer as combinações destes materiais, as qualidades e defeitos que cada um possui e a vantagem e desvantagem de utiliza-los. Também é necessário saber que há produtos iguais (que podem ser aplicados no mesmo sistema), porém feitos de materiais diferentes e com diferenças de preços gritantes.
Outra coisa fácil de se ver na população leiga e até entre profissionais desses ramos é que muitos não conhecem de fato o produto que estão utilizando (ou pelo menos insistem em utilizar termos errôneos). Um bom exemplo são as velhas juntas de vedação estáticas de cabeçotes de motores a combustão interna, que antigamente eram baseadas em Fibra de Amianto e que, pela legislação moderna, foram substituídas por Fibra de Vidro e ou Fibra de Aramida, porém até hoje são conhecidas por todos como “juntas de amianto” ou “juntas de papelão de amianto”. Outro exemplo são algumas peças de cerâmica - como por exemplo bocais de lâmpadas domésticas -, comumente chamadas informalmente de "louça" ou "porcelana", quando na verdade são materiais muito mais comuns e baratos.
Tanto descrevemos sobre materiais, citamos um punhado de aplicações, mas não nos aprofundamos muito em algumas informações tão relevantes quanto o que já foi publicado: as propriedades mecânicas!
Neste artigo foi concatenado uma grande quantidade de informações de vários sites e documentos técnicos sobre como os materiais se relacionam com a física, abordando vários exemplos práticos e links que dão acesso à vários outros artigos no blog!
De ínício precisamos saber uma coisa:

Em CTM, tenacidade é a capacidade de um material absorver energia e deformar permanentemente (plasticamente) sem fraturar.
A tenacidade requer um equilíbrio de resistência e ductilidade.
Segundo a tenacidade, um material pode ser:
1. Friável (frágil, quebradiço): Que pode ser quebrado ou reduzido a pó com facilidade. Ex: Vidros e cerâmicas;
2. Maleável: Pode ser transformado facilmente em lâminas, Ex. Ouro, Prata, Cobre;
3. Séctil: Pode ser facilmente dividido em pedaços com um objeto cortante. Ex Ouro, Prata, Cobre, Alumínio;
4. Dúctil: Pode ser transformado facilmente em fios. Ex. Ouro, Prata, Cobre;
5. Flexível: Pode ser dobrado, mas não recupera a forma anterior. Ex: Alumínio, Talco, Gipsita, Polipropileno, Polietileno, Poliamida (plásticos em geral);
6. Elástico: Pode ser dobrado mas recupera a forma anterior. Ex. Micas e Borrachas.
OBSERVAÇÃO: Uma confusão comum ao termo é achar que um material duro é também tenaz. Como exemplo temos o diamante, que só pode ser riscado por outro diamante (logo, extremamente duro), mas pode ser quebrado se sofrer uma requisição muito alta como uma martelada (logo, tem baixa tenacidade, flexibilidade).
Outra confusão também feita no dia-a-dia é com flexibilidade e elasticidade. A elasticidade não é uma propriedade que se aplica apenas à objetos borrachosos, e a flexibilidade não é 'sinônimo' de elasticidade. Mas isso veremos ao longo do texto.
Ductilidade e Fragilidade
Um material dúctil é aquele que se deforma sob tensão mecânica. O Ouro, o Cobre e o Alumínio são metais muito dúcteis. O oposto de dúctil é frágil, quando o material se rompe sem sofrer grande deformação.
A ductilidade é a propriedade que representa o grau de deformação que um material suporta até o momento de sua fratura. Materiais que suportam pouca ou nenhuma deformação no processo de ensaio de tração são considerados materiais frágeis. Isto é, quando, por exemplo, um plástico é rasgado ao meio, esse processo entre estica-lo até rasga-lo é chamado de ductibilidade, contudo, existe uma grande porcentagem de moléculas ultra finas que possibilitam a deformação elástica.

Imagem 1
Em metalurgia a ductilidade é a propriedade que apresentam alguns metais e ligas metálicas quando estão sob a ação de uma força, podendo estirar-se sem romper-se, transformando-se num fio. Os metais que apresentam esta propriedade são denominados dúcteis.
Os metais se caracterizam por sua elevada ductilidade, pelo fato de os átomos se disporem de maneira tal na sua estrutura que possibilitam o deslizamento de uns sobre os outros, permitindo o estiramento sem rompimento. A ductilidade de uma determinada liga metálica pode variar em função da sua microestrutura. A microestrutura varia em função do tipo de tratamento térmico e do tipo de processo de fabricação. Ligas quimicamente idênticas, portanto, podem apresentar comportamentos variando entre totalmente frágil e totalmente dúctil.
Este fato é de extrema importância para a indústria, que pode trabalhar com um material em sua condição dúctil e, após isto, trata-lo termicamente para que atinja as propriedades finais.
Ductilidade x Fragilidade
Ao especificar um material, é importante ter em mente que fragilidade e ductilidade são propriedades totalmente opostas: a tendência de um material a deformar-se significativamente antes de se romper é uma medida de sua ductilidade, e a ausência de deformação significativa antes da ruptura é chamada de fragilidade. Portanto, quanto maior a ductilidade, menor a fragilidade.
Com a chegada das normas envolvendo a redução de uso de materiais tóxicos, muitos setores da indústria tiveram que se adaptar, substituíndo elementos químicos considerados muito prejudiciais à vida por outros 'mais aceitáveis'. Foi o caso do Chumbo (Pb), um dos primeiros elementos da Tabela Periódica a entrarem na mira de normatizações, entre elas a famosa RoHS (Restriction of Certain Hazardous Substances), aplicada pela primeira vez na diretiva EC 2002/95/EC.
Pois bem, o Pb é o exemplo mais prático de ductibilidade. Conforme a temperatura de trabalho se eleva, ele tende a se deformar seguindo as forças impostas, e isso sempre foi ótimo para as soldas eletrônicas com base em Estanho (Sn), pois as faz suportar vibrações e até impactos.
Ainda hoje encontramos esferas de soldagem eletrônica feitas com ligas SnPb no mercado de reposição. Uma das ligas encontradas no varejo é a Sn(63%)/Pb(37%). No entanto, para o mercado OEM (fornecimento para fabricantes) o uso de ligas Estanho/Prata/Cobre (abreviadas pela sigla "SAC") é mais comum, já que todas as marcas de eletrônicos seguem o RoHS. O grande entrave é a ductibilidade e tenacidade menor, o que tende a gerar mais problemas com trincas nos Ball Grid Arrays a longo prazo.
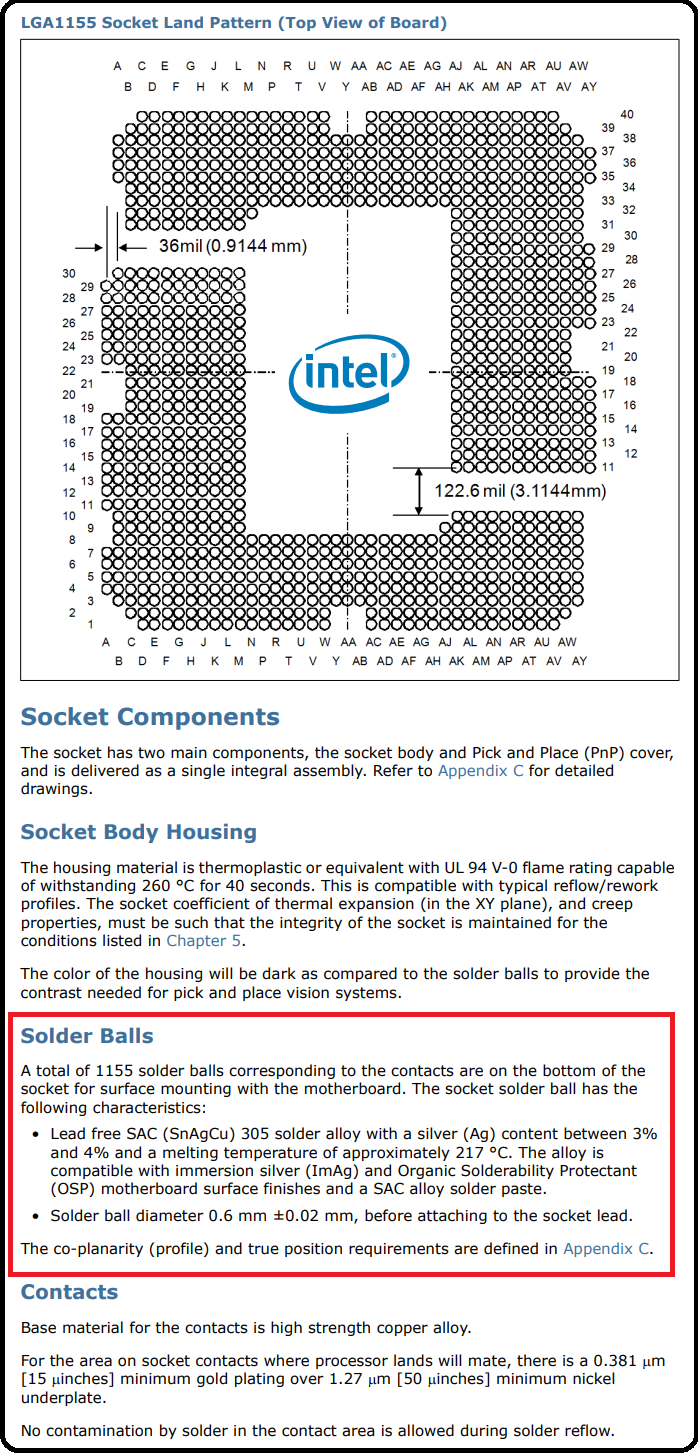
Complemento 1 - O uso de ligas SnAgCu nas soldas de circuitos eletrônicos livres de Chumbo
Maleabilidade
A ductilidade e a maleabilidade (capacidade de formar lâminas) de um material são duas propriedades relacionadas, já que as duas dependem do deslizamento dos átomos uns sobre os outros através de uma ação externa sobre o material.
A maleabilidade é uma propriedade que junto a ductilidade apresentam os corpos ao serem moldados por deformação. A diferença é que a ductibilidade se refere a formação de filamentos e a maleabilidade permite a formação de delgadas lâminas do material sem que este se rompa, tendo em comum que não existe nenhum método para quantificá-los.
O elemento conhecido mais maleável é o Ouro, que se pode malear até dez milésimos de milímetro de espessura. Também apresenta esta característica, em menor escala, o Alumínio, tendo-se popularizado o papel de Alumínio como envoltório conservante para alimentos, assim como na fabricação do Tetra Brik.
Em muitos casos, a maleabilidade de uma substância metálica aumenta com a temperatura. Por isso, muitos metais são trabalhados mais facilmente a quente.
Com as explicações acima, podemos introduzir outros parâmetros...

OBSERVAÇÃO: Com a intenção de se ter uma melhor compreensão do texto, recomendo a leitura do artigo "Física do movimento - PARTE 1", para que fique mais claro na mente o que é força, peso, inércia, atrito, massa, volume, densidade e movimento. Boa leitura!
Este tópico é permeado por cinco formas de aplicação de força em materiais: são elas:
→ Esforços axiais:
-> Tração;
-> Flexão;
-> Compressão.
→ Esforços transversais:
-> Torção;
-> Cisalhamento (tensão tangencial ou de corte).
De outra maneira, podemos classificar as tensões em tipos diferentes de esforços de cisalhamento. Observe:
→ Tensões normais (engloba Tração e Compressão);
→ Tensões transversais (Flexão);
→ Tensões torcionais (Torção).
A tensão é mais comumente usada quando a força é exercida para puxar um objeto (pense na tensão de um cabo de aço de um guindaste suspendendo um bloco), no entanto, ela pode ser usada na descrição de qualquer uma das forças acima listadas.
Em geral, quando se submete um material a um conjunto de forças se produz tanto flexão e ou torção, todos estes esforços conduzem a aparição de tensões tanto de tração como de compressão. Em outras palavras, todo esforço mecânico é composto por um conjunto de tensões normais.
Mas afinal, o que é cisalhamento?
Cisalhamento
No esforço de cisalhamento, (também chamado de tensão tangencial, ou ainda tensão de corte ou tensão cortante) é um tipo de tensão gerado por forças aplicadas em sentidos iguais ou opostos, em direções semelhantes, mas com intensidades diferentes no material analisado. Um exemplo disso é a aplicação de forças paralelas mas em sentidos opostos, ou a típica tensão que gera o corte em tesouras.
Um exemplo prático são molas de cisalhamento, confeccionadas em borracha e chapas de metal para aplicação alguns seletos tipos de suspensão de caminhões:
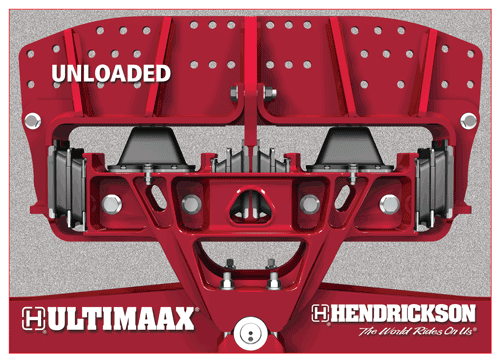
GIF 1 - O cisalhamento exemplificado com uma suspensão automotiva
Note que, quando a carga é aplicada o chassi é deslocado para baixo, tensionando as quatro molas de cisalhamento e comprimindo as duas molas de carga progressiva. Para tal efeito, tais molas devem ter uma ampla e resistente estrutura elastomérica entre as chapas (flanges e taxa). Para entender melhor, observe o Folder abaixo:
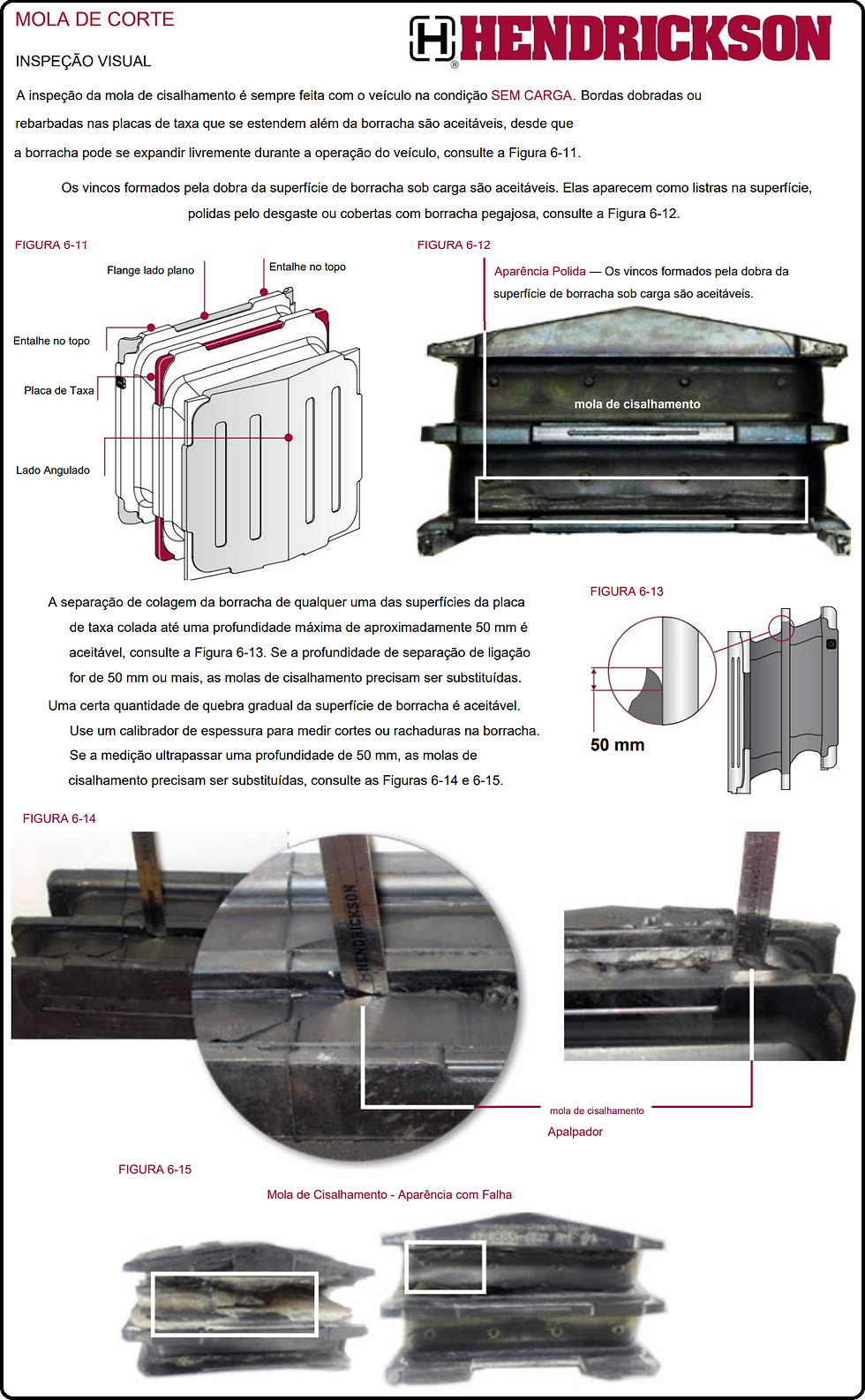
Complemento 2 - As molas de cisalhamento das suspensões Hendrikson UltiMaax e HaulMaax são feitas de lâminas de aço separadas por aplicações de borracha (em suspensões geralmente é aplicado NR pura, NR+BR ou NR+SR)
A partir deste tópico podemos expandir para outros tipos de tensão, afinal a flexão é um cisalhamento causado por cargas transversais e a torção é um cisalhamento causado por cargas torcionais!
Compressão
A compressão é gerada quando se empurra algo usando a força. Pense num cilindro preenchido de gás, pressurizado. O gás comprimido estará pressionando as peredes do vaso para o sentido cuja força contrária é inferior.
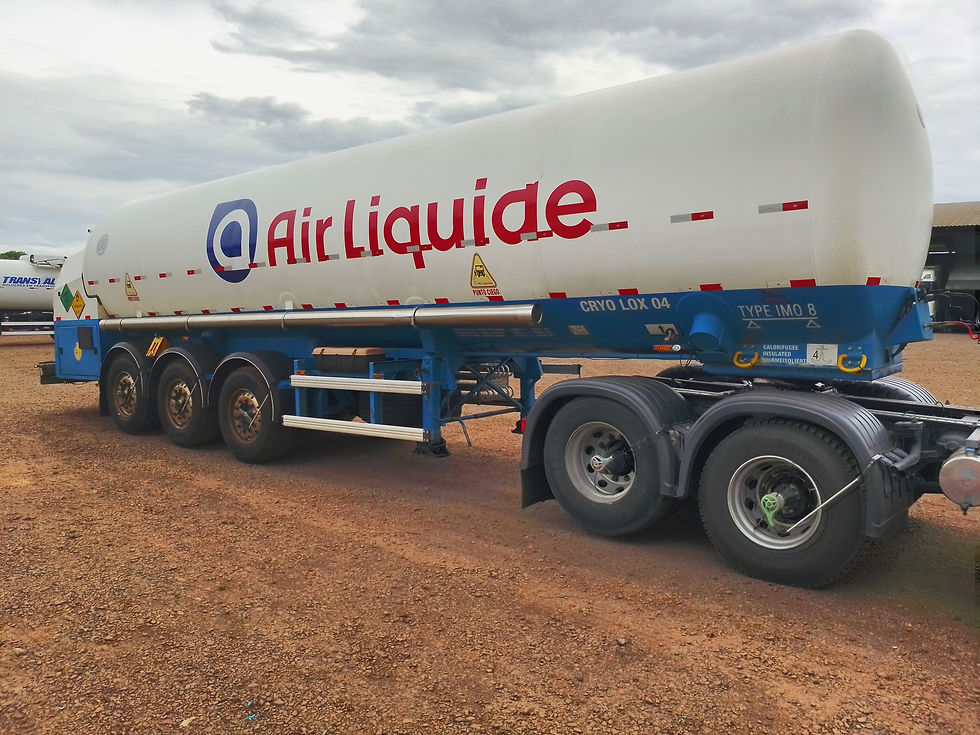
Imagem 2 - Cilindro para armazenamento de gases cuja pressão de trabalho é 300 kPa
Nas lâmpadas de baixa e alta pressão com vapor de Mercúrio ou vapor de Sódio também pode se notar forças de compressão...

Imagem 3 - Lâmpada fluorescente de uso doméstico. Está é de baixa pressão e com vapor de Mercúrio
Para se ter uma ideia, a pressão atmosférica ao nível do mar é de 1 ATM (atmosfera), ou seja, cerca de 101.3 kPa. Se pegarmos uma lâmpada de vapor de Mercúrio e gás Argônio sob alta pressão, teremos entre 2 e 4 ATM para o metal vaporizado e em torno de 0,03 ATM (3.039 Pa) para o gás de partida. Já uma lâmpada de vapor de Sódio com gás inerte sob baixa pressão deve conter o vapor metálico na casa dos 7x10^-7 ATM e gases Neônio e Argônio na casa dos 7x10^-4.
Como podemos notar, enquanto as de alta pressão possuem este nome pois operam acima da pressão atmosférica, as de baixa pressão operam abaixo dela.
Para saber mais sobre lâmpadas fluorescentes, comece CLICANDO AQUI!
Propaganda de conteúdo relacionado do HC!
Clique na imagem acima para saber mais detalhes sobre as características estruturais do cinescópio das velhas TVs de tubo!
Motores de combustão interna também trabalham com compressão em seus cilindros. Atualmente, o mais comum na indústria são propulsores de 4 tempos:
-> Admissão:
-> Compressão:
-> Combustão:
-> Exaustão.
Como podemos ver, a transformação da mistura A/C em movimento - e principalmente calor - ocorre no terceiro tempo. Nesta fase e na anterior - a compressão -, o motor precisa ser dimensionado para lidar com altos valores de pressão em seus cilindros, caso contrário, os parafusos que seguram o cabeçote sobre o bloco - ou até mesmo a estrutura do próprio cabeçote - podem ceder e tudo ir para os ares.
Ainda assim, apesar da indústria já utilizar fixadores de deformação plástica (e você verá mais detalhes sobre na sequência deste texto), é tolerável uma "micro-vibração" do cabeçote e da sua vedação sobre o bloco (lembre-se que entre os dois há uma junta de estanquiedade), ou seja, existe um movimento imperceptível entre estas peças, e este movimento é limitado pela carga dos parafusos que juntam as três peças.
Pois bem, um movimento do cabeçote para cima iria fazer com que a sua junção com o bloco perdesse a estanquiedade, misturando líquido de arrefecimento com óleo lubrificante e deixando escapar parte da mistura A/C. Claramente isso deve ser evitado, e por isso que cabeçotes individuais (um para cada cilindro) estão cada vez mais em desuso em decorrência da cada vez maior taxa de compressão dos motores de combustão interna:

Imagem 4 - Perceba os seis cabeçotes do motor DC13, da Scania
Em automóveis de passeio e pequenos veículos de carga / passageiros os cabeçotes individuais nunca foram comuns, entretanto, em máquinas agricolas / construção e caminhões / ônibus isto já foi demasiado comum (por questões de valores, espaço e manutenção), todavia, vem perdendo espaço, e um dos movimentos mais recentes foi por parte da Scania, que passou a aplicar um cabeçote inteiriço sobre todos os cilindros nos recentes motores Super, justamente pela taxa de compressão bastante alta (25 MPa é a pressão da injeção de combustível na câmara), que fez com que os cabeçotes se deslocassem para cima durante testes de laboratório.

Imagem 5 - Perceba o cabeçote inteiriço
Como já foi dito, adiante você verá detalhes sobre os parafusos elásticos e os de deformação plástica. O que vimos neste tópico pode ser um bom embasamento para entender o uso de tais fixadores nos motores atuais. Quanto maiores as forças envolvidas e a possibilidade de vibração, maior deve ser o cuidado com o afrouxamento de peças, que obviamente levam à grandes problemas.
Tração
Já a tração é uma força de contato que é transmitida através de um meio físico capaz de puxar objetos. Em palavras simples, se a compressão "empurra", a tração "puxa".
Pegue como exemplo o semi-reboque da imagem acima: quem detém a capacidade de tracionar é o rebocador, isto é, o caminhão-trator. Através de um meio físico, ou seja, um acoplamento - composto por quinta-roda, mesa e pino-rei - ele consegue tracionar o semi-reboque. O trailer é dependente de alguém que o puxe.

Imagem 6 - Esta é a mesa e pino-rei que os semi-reboques possuem para serem 'puxados'
No caso da imagem acima, não há cordas ou cabos tensionados, mas sim os componentes do acoplamento, que precisam resistir a todas as forças aplicadas. Repare que, um semi-reboque carregado descendo uma serra gerará uma grande força de compressão sobre o acoplamento caso os freios do conjunto não estiverem em perfeita 'sintonia'.
A capacidade de tração de uma quinta-roda, definida como "valor D", é dada pela seguinte equação:

Complemento 3 - Como se calcula a capacidade de tração de uma quinta-roda
Através do exemplo acima (usando a 2° Lei de Newton, ou seja, o valor de tração é obtido multiplicando a massa pela sua aceleração), fornecido pela Jost, podemos concluir que uma capacidade de tração de 197,4 kN (kiloNewton) equivale à 20,129 kgf (kilograma força), ou seja, cerca de 20,1 toneladas. Parece pouco, no entanto, não estamos nos referindo à capacidade de carga de um veículo, mas sim da capacidade de um acoplamento em puxar cargas.
OBSERVAÇÃO: Note que até mesmo em documentos técnicos há a confusão entre peso e massa. O correto na descrição das variáveis seria "massa total máxima permitida no veículo trator (ton.)" e "massa total máxima no semi-reboque (ton.)".
Para saber mais sobre a construção das quintas-rodas, bem como de ligas metálicas utilizadas na construção de semi-reboques, vasos e tanques de implementos rodoviários, recomendo que CLIQUE AQUI! (uso de plásticos e borrachas na industria automotiva), CLIQUE AQUI! (Aço-Carbono e Ferro Fundido) e CLIQUE AQUI! (Aço baixa, média e alta liga e muito mais).
Flexão
O esforço de flexão ou Momento Fletor é um caso particular de tração e compressão agindo juntos na mesma seção, causando deformações predominantes nas faces opostas do corpo ou estrutura e menores deformações e consequentes tensões na parte central, se anulando no seu eixo de inércia.
O conjunto de pontos de tensão nula no interior do copo flexionado é denominado Linha neutra.
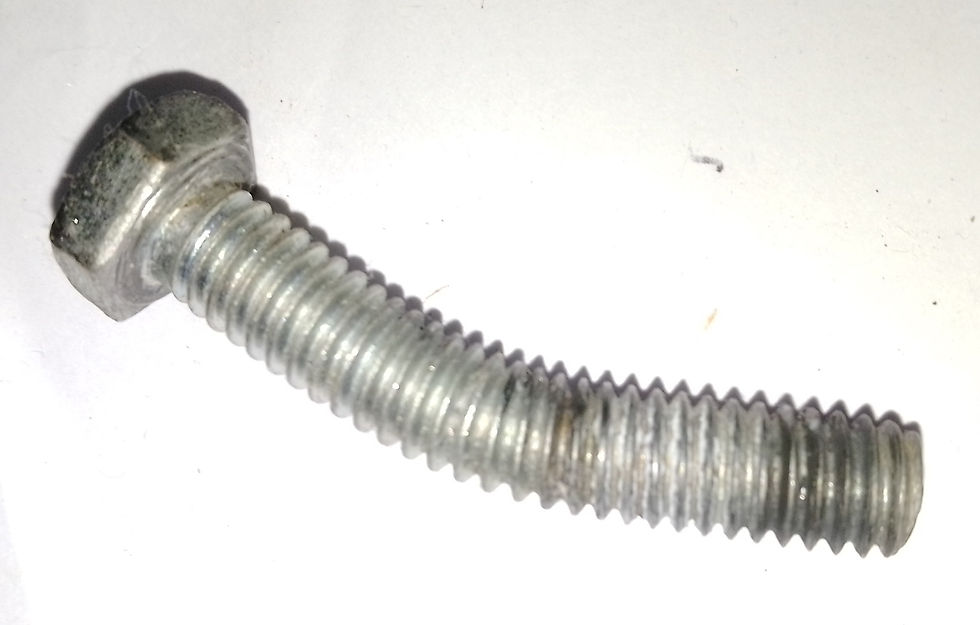
Imagem 7 - Um parafuso que sofreu flexão
O parafuso da imagem acima foi flexionado a ponto de deformar-se, se mostrando até bastante dúctil. Em sua cabeça não havia especifícação alguma, portanto, não podemos saber se ele era de classe 4.8, 5.8 ou 8.8, por exemplo.
Este esforço de flexão mostra também que o parafuso ultrapassou sua fase elástica e entrou em deformação plástica. Mais um pouco de deformação ele iria atingir sua tensão de ruptura.
Observe a próxima figura:

Imagem 8 - Suspensão do tipo 'bogie', com apenas dois feixes (um de cada lado) para dois eixos
Um conjunto de lâminas empilhadas - em geral arqueadas - e com algum grau de elasticidade forma o feixe de molas, que através da flexão sustenta a massa do veículo sobre os eixos e absorve impactos de rodagem.
Observando um aparelho de ar-condicionado split de uma casa, notei que sua base era feita de PP reforçada com 20% de Talco, suportando a serpentina de condensação, dois motores monofásicos, ventoinha, compressor, tubulação e parte elétrica. Esta base estava apoiada em dois suportes metálicos de fixação na parede, e é visível a flexão da estrutura de plástico:

Imagem 9 - Perceba a geometria complexa da base. Se trata de um Electrolux VI12R
Apesar de ser feita de plástico com carga mineral, seu formato geométrico complexo, autoreforçado, a permite suportar todos os componentes da unidade externa de refrigeração, além da vibração natural deste sistema quando em funcionamento. Aqui, a única forma de se obter rachaduras é através do ressecamento do plástico ocasionado pela constante exposição às condições atmosféricas, mesmo se levando em conta os aditivos anti-UV e antioxidantes presentes no compósito (ok, talvez isto leve muito mais que um década para ser observado). Como este equipamento está há anos disposto no mesmo lugar e sob às mesmas condições ambientais, a base dificilmente perderá esta deformação ao ser trocada de posição.
As placas de circuito impresso (PCBs), em geral feitas de Fenolite ou FR4 possuem algum grau de elasticidade, proporcionando mais resistência à vibrações e choques mecânicos, no entanto, os componentes soldados à elas precisam também suportar isso.
CURIOSIDADE: Para saber mais sobre a composição química e características elétricas das placas de circuito, CLIQUE AQUI!
Se tratando de componentes cerâmicos SMD, temos o ponto 'frágil' do tema!

Imagem 10 - Simplificação de um teste de flexão de PCB com um SMD soldado
Cerâmicas são literalmente frágeis, e componentes SMD feitos de tal classe de materiais soldados a uma placa de circuito são frequentemente vulneráveis a rachaduras por expansão térmica ou tensões mecânicas, mais do que componentes PTH.
As rachaduras podem vir da linha de montagem (de máquinas automatizadas) ou de alta corrente elétrica no circuito (maior geração de calor por efeito Joule). Vibração e forças de choque na placa de circuito são mais ou menos transmitidas sem amortecimento para os componentes e suas juntas de solda, e força excessiva pode fazer com que um capacitor destes quebre. O excesso de solda nas juntas é indesejável, pois pode aumentar as forças a que o condensador está sujeito.
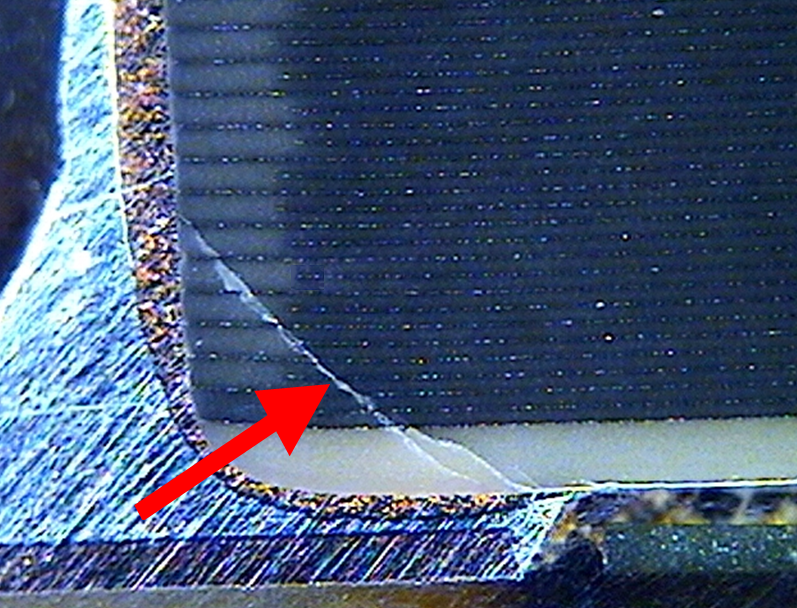
Imagem 11 - Micrografia da cerâmica quebrada em um capacitor MLCC
CURIOSIDADE: A capacidade dos capacitores MLCC de resistir ao estresse mecânico é testada pelo chamado teste de flexão de substrato, em que um PCB com um MLCC soldado é dobrado por um punção de 1 a 3 mm. A falha ocorre se o MLCC entrar em curto-circuito ou mudar significativamente na capacitância.
As resistências à flexão dos MLCC diferem pelo material cerâmico, pelo tamanho do componente e pela construção física dos capacitores. Sem mitigação especial, os componentes MLCC de cerâmica NP0/C0G Classe 1 atingem uma resistência à flexão típica de 2 mm, enquanto os tipos maiores de cerâmica X7R, Y5V Classe 2 atingem apenas uma resistência à flexão de aproximadamente 1 mm.
Para saber mais sobre capacitores cerâmicos em geral, CLIQUE AQUI!
Peças menores, como o invólucro 0402, atingiram em todos os tipos de cerâmica maiores valores de resistência à flexão.
Para saber mais sobre invólucros SMD de capacitores, CLIQUE AQUI!
Voltando ao assunto placas de circuito impresso, achei relevante citar uma falha descoberta recentemente em algumas PCBs de adaptadores gráficos da Gigabyte, mais especificamente da série RTX30 (Ampere) e RTX40 (Ada Lovelace). Se tratam de trincas no fim do conector PCIe x16, próximo à trava do slot:

Imagem 12 - A Gigabyte nega a garantia e devolve as placas com a seta indicando a trinca. Créditos: Louis Rossmann/eBay
Segundo sites de notícias, as trincas são mais frequentes em PCs vendidos prontos, isto é, montados, no entanto, é consenso que os adaptadores gráficos estão cada vez maiores em espessura e comprimento e apenas a PCB de FR4 se torna pouco para sustentar todo o sistema, necessitando de carenagens na parte de trás das placas, bem como nas laterais, que acabam sendo vistas mais como "embelezadoras" do que estruturais. Um bom exemplo do tamanho absurdo de muitas placas de vídeo atuais é a Zotac RTX4090 PFG, com seus 38,1 cm de comprimento e 7,5 cm de espessura:

Imagem 13 - As placas para a linha RTX4xxx possuem um tamanho descomunal. Observe as carenagens que envolvem a PCB, o dissipador e os fans
Outro fator é o slot PCIe, que em placas-mãe mais parrudas já possui uma armação de metal por dentro da carcaça de plástico LCP com vários pontos de ancoragem na PCB, para ser além de uma conexão de dados também um apoio estrutural para os cartões gráficos, afinal, apenas o PCIe de plástico com seus 10,5 cm de comprimento não iria dar conta.
CURIOSIDADE: Para saber mais sobre a composição e estrutura dos slots PCIe, CLIQUE AQUI!
A questão aqui, no caso da Gigabyte, é que o FR4 foi tensionado, isto é, sofreu esforços de flexão, e não aguentando, abriu fissuras num ponto específico da peça...

Imagem 14 - Uma Gigabyte RTX4090 vista por trás e a região problemática destacada pelo dedo do Youtuber Jayz2cens
Tanto a fragilidade estrutural quanto a vibração gerada pelas ventoinhas podem ter colaborado para a falha, no entanto, como foi repassado, os casos são mais comuns em PCs vendidos pré-montados, indicando o agravante da falha de manuseio e ou montagem. Essa citação não serve para criticar, mas sim como um exemplo prático de ação da força de cisalhamento transversal.
Mais uma vez, pulando pro 'galho' da mecânica, os tirantes de barra estabilizadora são desenvolvidos para serem o 'elo frágil' do sistema, também tendo uma boa elasticidade, entretanto, entortanto ou quebrando em situações extremas de estresse mecânico (compressão e distenção) afim de preservar a barra e demais componentes da suspensão. Levando isso em conta, podemos observar que aquelas bieletas construídas com compósitos poliméricos utilizam resinas cuja resistência à tração, compressão e ao impacto é muito baixa, mas é possível elevar essas propriedades reforçando-as com fibra de vidro, melhorando muito a tenacidade, e isso somado à sua geometria treliçada (ou algo semelhante a uma viga Vierendeel) tornam-as ideais para a aplicação em veículos leves.
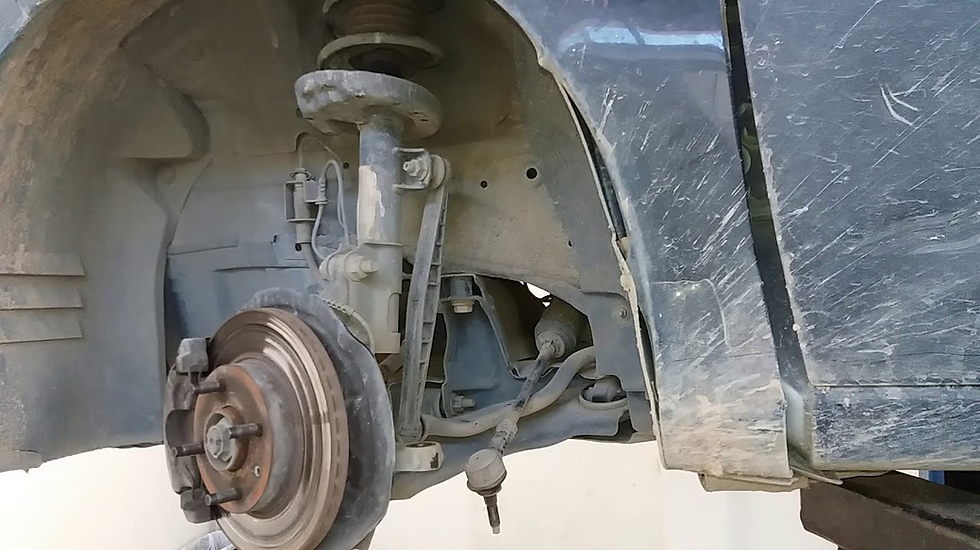
Imagem 15 - GM Spin, Onix, Prisma e Cobalt fazem uso de uma bieleta feita de >POM-GF25<
Veja abaixo a foto mais detalhada deste modelo de bieleta. Lembre-se que estamos falando apenas de peças genuínas de reposição ou originais de fábrica:

Imagem 16 - Como o POM tem um coeficiente de atrito até favorável, o pino de ponta esférica de cada pivô fica em contato direto com a estrutura de POM-GF25, que tem a região usinada e engraxada para ter a menor aderência possível e maximizar a vida útil da articulação
Em geral, faz-se uso de PA66-GF30 nestas bieletas, como vemos nestes modelos da VW:

Imagem 17 - Bieletas aplicadas no Polo, Virtus, T-Cross e Nivus
A linha GM substituiu o POM-GF25 em prol do PA66-GF30 também:

Imagem 18 - A geometria da peça 'faz 50% do trabalho', já que as características deste tipo precisam estar niveladas com àquelas bieletas com haste cilíndrica em liga de aço. Alguns produtos paralelos usam uma haste treliçada em PA66-GF30
CURIOSIDADE: Como o PA66 tem um coeficiente de atrito até favorável (você verá isso na PARTE 2 deste texto), ele já é amplamente utilizado como bucha para o pino de ponta esférica em pivôs de bandeja, terminais de direção e bieletas, logo, tirantes de PA66-GF30 sofrem apenas uma usinagem nas pontas para abrigar a articulação, assim como as supracitadas bieletas de POM-GF25.
Para entendermos as especificações de elasticidade e plasticidade tanto das bieletas articuladas com o corpo em liga de aço quanto das com o corpo de compósito plástico, vamos começar pelo sistema mais rudimentar: as 'bieletas parafuso', mostradas anteriormente.

Imagem 19 - No Focus de primeira e segunda geração, a Ford utilizou parafusos classe 8.8 ou 9.8 (tipo obsoleto na indústria) como tirantes de barra estabilizadora
Como já visto, um parafuso 8.8 possui uma resistência à tração (LRT) minímo nominal de 800 N/mm³ (800 MPa), enquanto seu escoamento (LE) é a partir dos 640 N/mm³ (640 MPa). Já um 9.8 possui LRT de 900 MPa, com LE iniciando aos 810 MPa. Tais parafusos podem ser construídos utilizando-se de aços médio ou alto Carbono (SAE 1040 pra cima) ou também aço microligado. O processo de têmpera é obrigatório para garantir as propriedades de tração, elasticidade e escoamento classificadas.
Isso significa que os tirantes articulados, sejam em liga de aço ou compósito plástico não fogem muito destes valores, afinal, a parte central da haste é que deverá aguentar a flexão ocasionada por compressão ou tensionamento ocasionado por tração, se deformando e até quebrando em situações extremas, para preservar os demais componentes. Neste ponto, um aço SAE entre 1040 e 1080 já daria conta.
Vídeo 1 - Note a plasticidade da haste metálica. Perceba também que a força para entortar o pequeno parafuso 8.8 (de uso geral) precisa ser maior - afinal, a alavanca é bem mais curta -, por isso que só foi possível deforma-lo utilizando-se de um martelo
O ponto em que quero chegar é que um simples parafuso 8.8 com arruelas de metal e borracha já dá conta do recado em vários projetos, e trabalhando a geometria das hastes confecionadas em PA66-GF ou POM-GF é possível se obter tirantes articuladas super leves, com boa tenacidade e apropriados para este fim.
Torção
No esforço de torção predomina a tensão de cisalhamento angular, e como na flexão, causa maiores deformações e consequentes tensões nas faces ou bordas externas da peça, corpo ou estrutura, se reduzindo na parte central onde as deformações são menores, se anulando na linha neutra localizada no eixo de inércia, onde não há deformação.
Quando se aperta um parafuso, a chave sofre com esforço de torção, ainda mais no momento do aperto final, onde o parafuso já se "recusa" a girar mais um 'teco' e você, na emoção, tenta forçar mais um pouquinho. Perceba que aqui a chave também precisa ter um grau de elasticidade para não se deformar ao ser forçada ao máximo!
E de que adianta ter falado dos tirantes sem falar das barras estabilizadoras?
A barra estabilizadora promove uma conexão entre as duas rodas de um eixo. Sempre que estas são impostas a cargas iguais, vão se deslocar verticalmente com o mesmo curso, ou seja, não haverá movimento relativo entre as rodas. Entretanto, quando as rodas são expostas a cargas desiguais, como em curvas, ocorre o movimento vertical relativo. Esse movimento provoca a torção da barra, que resiste ao movimento relativo das rodas.
Dessa forma, o estabilizador limita a rolagem da carroceria, além de ter considerável influência no comportamento em curva do veículo. Com isso, é possível reduzir a carga das molas, deixando o veículo mais suave ao passar sobre irregularidades em linha, mas firme quando contornando curvas.
Duas variações de barras estabilizadoras são as mais utilizadas. Não há diferenças em seu funcionamento, apenas nas conexões com a suspensão. A primeira variação é bastante utilizada no eixo dianteiro de carros de baixo custo / compactos e no eixo traseiro de alguns carros 'mais desenvolvidos'.
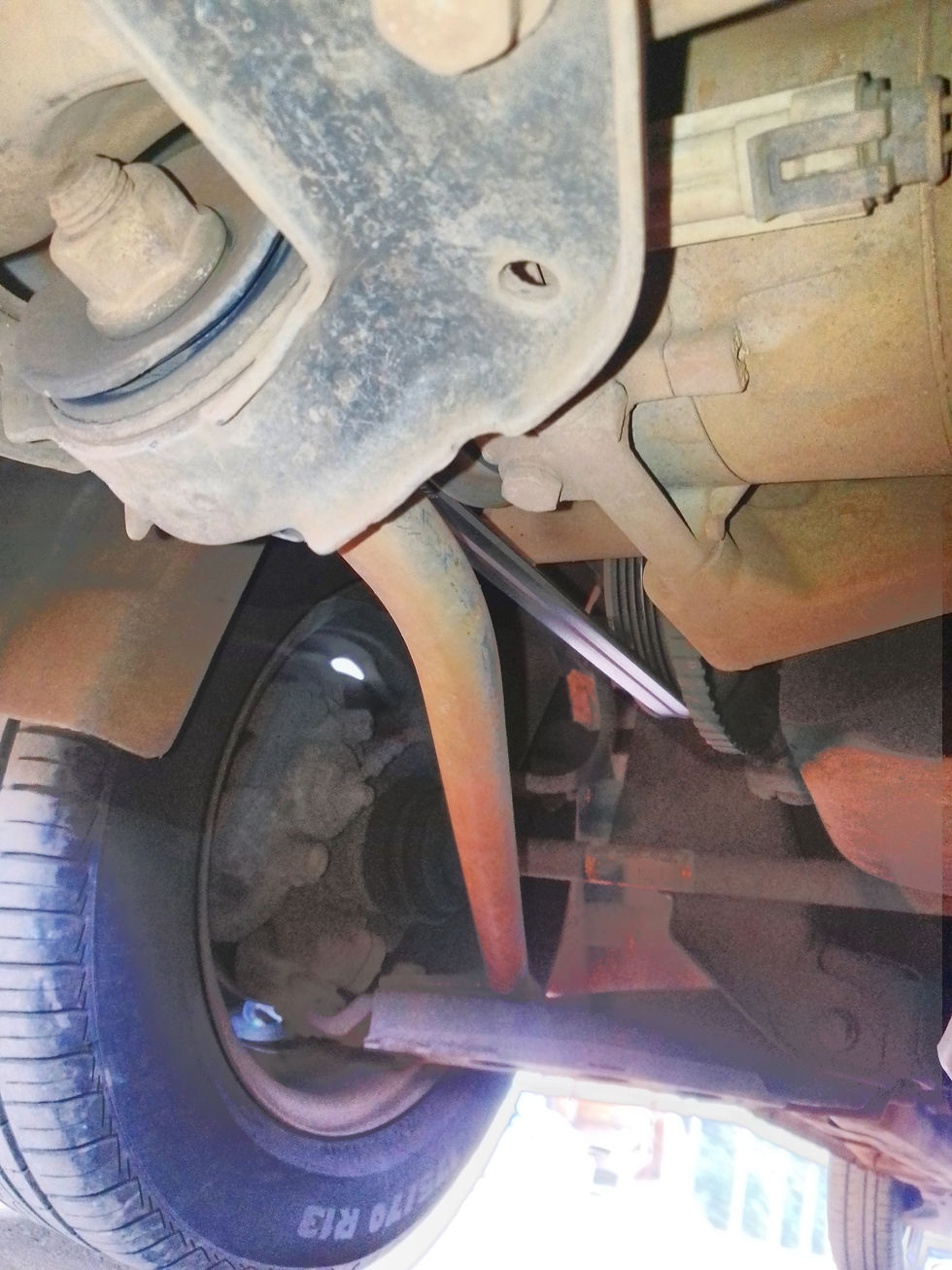
Imagem 20 - O Chevrolet Celta sequer tem casquilhos de borracha nas bandejas, muito menos uma barra estabilizadora inteiriça
A barra é fixada na estrutura do veículo (em geral no subchassi) por um par de casquilos de borracha e abraçadeira, e se conecta às rodas através dos braços de suspensão, isto é, das bandejas, onde ao menos uma abraçadeira e um casquilho de borracha fixa cada ponta da barra estabilizadora.
Uma característica desse método é a dificuldade de montagem, que por vezes requer mais de um técnico para tal. Essa fixação na bandeja provoca uma tensão a mais na barra estabilizadora, que nem sempre se traduz em um bom acompanhamento desta aos movimentos de cada lado da suspensão. Nesta aplicação a relação entre o ângulo de torção da barra e o curso da suspensão não favorece a sensibilidade do conjunto, prejudicando o efeito quando um lado está em compressão e o outro em distensão.
Este sistema é encontrado nos Renault Scénic e Mégane de primeira geração, tanto os Phase 1 quanto os Phase 2. Há uma barra fixada ao agregado com casquilhos de borracha e abraçadeiras, e suas pontas são fixas por debaixo das bandejas com abraçadeiras e casquilhos de borracha (e dá um trabalho suado pra montar sozinho).
No caso de suspensões traseiras, o uso de um parafuso com buchas elásticas pode ser usado entre a bandeja e a barra.

Imagem 21 - Esta é a suspensão traseira independente de um Focus MK1.5 ano 2006. Com base nestas 'bieletas parafuso', podemos tirar algumas outras conclusões mais adiante neste texto. Repare nas abraçadeiras e casquihos que fixam a barra no agregado
Esta concepção também já foi aplicada na dianteira de veículos antigos, como é o caso do Chevrolet Chevette e de sua variante picape, a Chevy 500:

Imagem 22 - Uma Chevy 500 ano 1991 com um rudimentar sistema de 'bieletas parafuso' com arruelas de metal e borracha
O KIA Bongo faz uso tanto de uma "semi-barra" (tal como no Celta), quanto de uma barra estabilizadora inteiriça, cujas bieletas são como na Chevy 500:

Imagem 23 - A seta laranja indica a bieleta, a amarela indica a semi-barra e a seta azul a barra estabilizadora
Outra aplicação em veículos, é a utilização de tirantes com pontas articuladas (conhecidas como bieletas, ou pendulum bar) para conexão da ponta da barra estabilizadora com o amortecedor estrutural. Nesta, o estabilizador mantém seu característico perfil U, mas suas extremidades possuem a interface com o pivô da bieleta. Dessa forma, previne-se as pontas da barra estabilizadora de pequenos esforços de flexão, aproveitando ao máximo sua função de alavanca para provocar torção. Além disso, essa configuração reduz o esforço na barra quando as rodas se movem simetricamente.
Em caminhões, muitos projetos eliminam os tirantes com pontas articuladas em prol de apenas um tirante com buchas de borracha, como vemos na imagem a seguir:

Imagem 24 - Na figura superior, um VW Meteor 6x4. Na figura inferior, um Scania R540 6x4. Ambos tem suspensão traseira com feixe de mola tipo bugie
No caso das imagens acima, uma inclinação do chassi em curvas, resulta numa flexão menor dos tirantes. Quem mais sofre é a barra estabilizadora, que assim como nos carros, se torce na região central, entre os dois casquilhos de borracha.
Alguns caminhões usam bieletas - em geral aqueles com suspensão pneumática - comparáveis aos automóveis:

Imagem 25 - Na figura da esquerda, a bieleta do eixo dianteiro de um VW Gol G5. Na figura da direita, a bieleta em um dos eixos traseiros de um Volvo FH 540
Note que o caminhão Volvo FH e no VW Meteor a barra estabilizadora é fixa no eixo e o tirante liga-a ao chassi. Já no Scania R540, a barra é fixada no chassi, e o tirante liga-a ao eixo. Nos automóveis ela é sempre fixada no sub-chassi e conectada às torres ou bandejas de suspensão pelos tirantes (ou simplesmente casquilhos de borracha com abraçadeiras, como na Renault Scénic 1 e Megane 1).
Barras estabilizadoras são construídas em aço mola, possuem perfil cilíndrico e sempre dispostas em forma de "U", tendo um módulo de elasticidade amplo para aguentar a torção.
Aço mola é uma designinação um tanto genérica, entretanto, resume uma pluralidade de ligas que, quando tratadas termicamente, servem muito bem pra função. É o caso dos aços com médio e alto teor de Carbono, tais como aqueles entre o SAE 1050 e o SAE 1120.
Outro material que pode ser utilizado em barras estabilizadoras ou até em bandejas de suspensão é o 15CDV6, um aço Cromo-Molibdênio-Vanádio que combina um alto limite de escoamento (superior ao SAE 4130, que também pode ser aplicado em barras estabilizadoras) com boa tenacidade e soldabilidade. O 15CDV6 pode ser facilmente soldado com muito pouca perda de propriedades durante a soldagem e sem a necessidade de tratamento térmico adicional.
Abaixo, a composição química do 15CDV6:

Tabela 1 - Note que se trata de um aço de baixo ter de Carbono, todavia, sua composição química permite tempera, tornando-o bastante diferente das ligas SAE 1006 ~ 1030
Agora, observe a comparação de composição química entre outros dois aços aplicados em molas e barras estabilizadoras:

Tabela 2 - O SAE 4130, 4340, 6150 e o 9254 são comuns para a construção de molas dos mais variados tipos. Lembrando que há um processo de tratamento térmico envolvido
CURIOSIDADE: Até mesmo o aço INOX 304, 304L, 316 e 316L podem ser utilizados na fabricação de molas, desde que passem pelo tratamento térmico adequado.
OBSERVAÇÃO: Quando é dito o termo “barra de torção”, estamos fazendo referência apenas à seção transversal da barra estabilizadora, pois esta é, de fato, uma barra de torção. O desenvolvimento da barra estabilizadora, o cálculo de rigidez / elasticidade da barra de torção leva em consideração seu comprimento, e essa variável não deve ser confundida com o comprimento total da barra estabilizadora.
Mudando um bocado o assunto, é interessante notar a capacidade de torção de um chassi de carreta sem que ocorra sua ruptura.
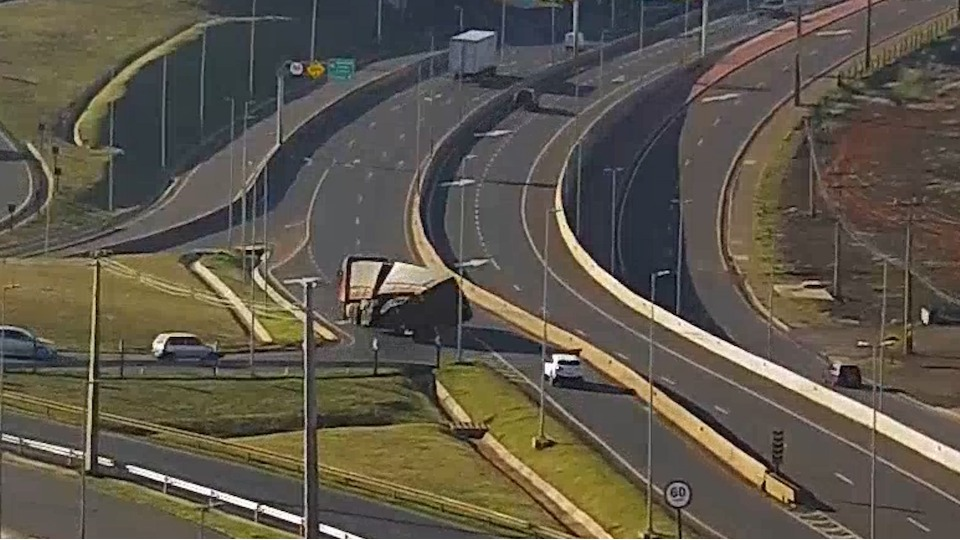
Imagem 26 - Tombamento de carreta ao fazer uma curva
Tanto é que muitas vezes o esforço de torção gera um empenamento no chassi, isto é, se nota uma flexibilidade grande, e para isso é necessário alinha-lo novamente torcendo-o para o lado oposto...

Imagem 27 - Um chassi de semi-reboque sinistrado e o resultado após a reforma
Os semi-reboques apresentam uma vantagem em relação aos veículos que os tracionam. Dada sua maior rigidez estrutural nas longarinas e suas ligações, a quinta-roda não precisa de uma mesa para ser afixada. Em geral, as sapatas são simplesmente parafusadas nas longarinas:

Imagem 28 - Os semi-reboques não precisam de uma mesa para a quinta-roda
Como a rigidez do prato e das sapatas é muito grande - estamos falando de componentes construídos em ligas de ferro fundido (comumente, FF Nodular) ou aço fundido -, para se evitar fissuras nestas peças, os fabricantes de caminhões comumente optam pela colocação de uma mesa sobre o chassi, já que a elasticidade do quadro tende a ser bem maior:

Imagem 29 - Repare na mesa ondulada onde as sapatas estão fixadas
Por falar em chassi, a travessas que interligam as longarinas também limitam a torção (isso é um bocado óbvio). Em geral, são componentes feitos de mesmo material que as vigas principais, exceto por alguns projetos que usam ferro fundido, como é o caso dos Scania.

Imagem 30 - Em amarelo a travessa em FF, e em azul a mesa da quinta-roda (por baixo da mesa há outra travessa de FF)
Em alguns projetos mais atuais da Scania, até mesmo a quinta-roda perdeu a mesa em prol de uma grande estrutura confeccionada em ferro fundido unindo longarinas e fazendo suporte dos eixos traseiros:
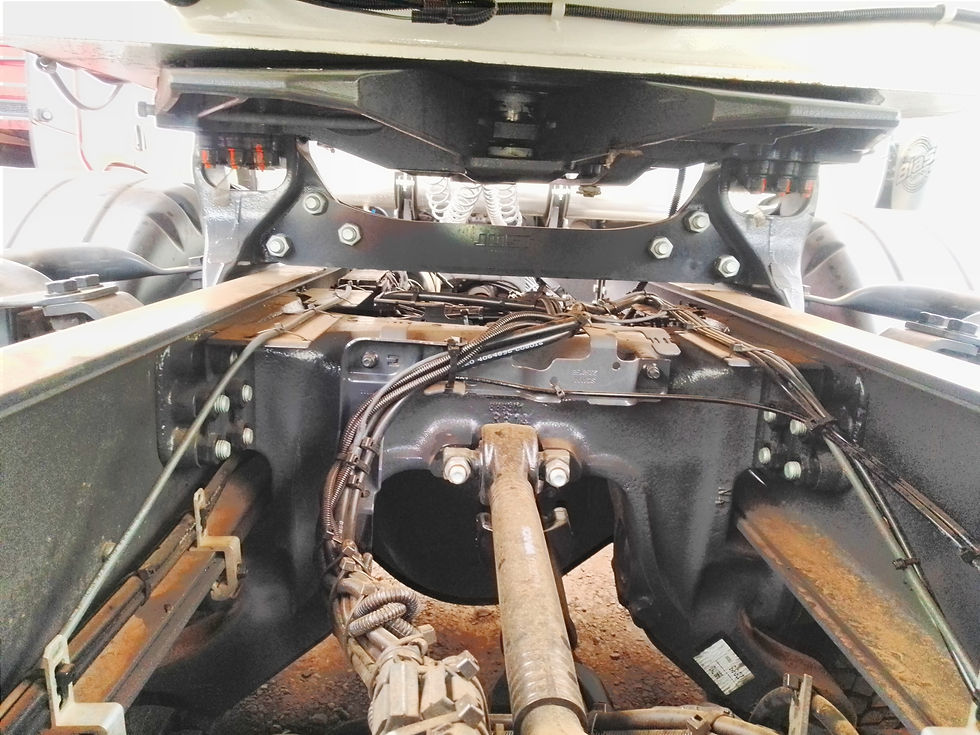
Imagem 31 - Perceba que as sapatas da quinta-roda são interligadas por uma barra limitadora de torção. Se trata de um Scania R540 6x4 ano 2022
O uso de suportes de eixo traseiro confeccionados em liga de FF é comum, entretanto, o usual são peças individuais, isto é, que não operam como limitador de torção unindo longarinas, como vemos neste Volvo FH 540 6x4 ano 2022:

Imagem 32 - Da mesma forma que o Scania da imagem anterior, este Volvo tem suspensão com feixe de molas tipo 'bogie'
Como vemos na imagem acima, a travessa que une as longarinas e também apoia os susportes de eixo é feita de chapas de aço, tal qual seus concorrentes, e diferente da Scania, que sempre coloca junções em FF (logo na sequência da caixa de câmbio e debaixo da quinta-roda). Na seguinte imagem, um Volvo FH 6x2 datado de 2021:
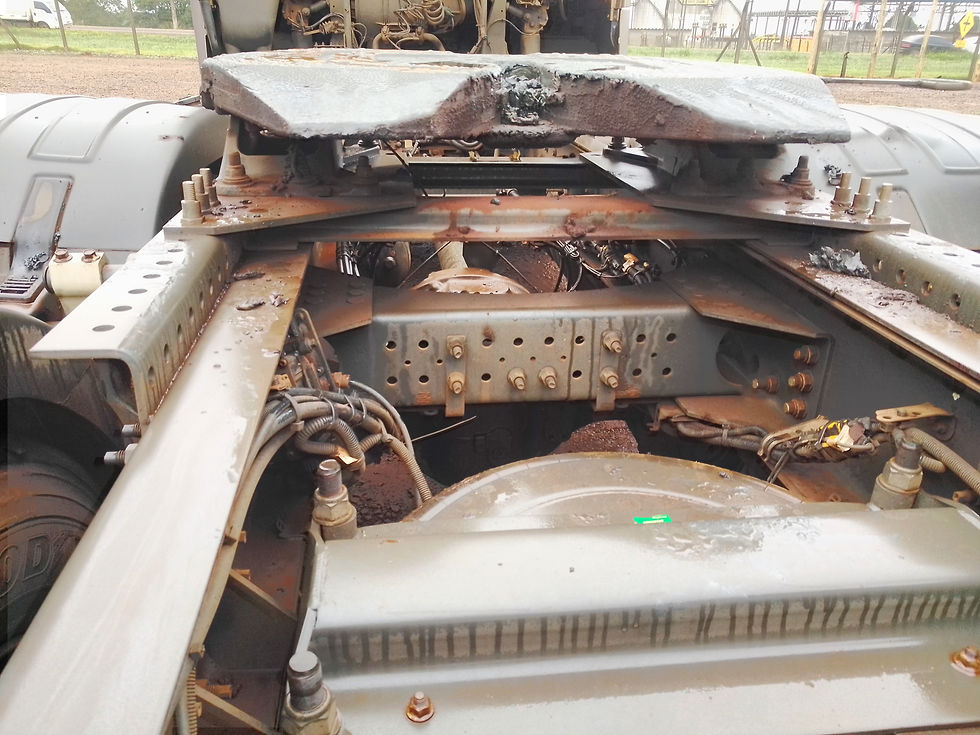
Imagem 33 - Note uma mesa mais simplificada e uma junção de longarinas feita de chapa de aço de perfil tubular
O interessante é que as duas soluções funcionam perfeitamente bem, todavia, fica a questão: Qual é mais cara de se produzir e qual a massa envolvida nas duas concepções de chassi?

Dado o tamanho e complexidade do texto, foi melhor dividir em mais uma parte para que mais informações possam ser adicionadas!
Quanto à teoria por trás de tudo o que foi mostrado até aqui, você pode CLICAR AQUI! e acessar a continuação do texto, para ter uma noção sobre deformação elástica, plástica, resistência à tração e vibração.
Gostou do artigo? Achou algum problema? Ficou com dúvidas? Entre em contato com Hardware Central pelo Facebook ou pelo e-mail hardwarecentrallr@gmail.com.
FONTES e CRÉDITOS
Texto: Leonardo Ritter.
Imagens, Vídeos, Gráficos e Diagramas: Leonardo Ritter; Hendrickson; Google Imagens.
Referências: Sabó; Mundo Educação; Brasil Escola; Hendrickson; Fontaine International; Jost Brasil; Sonelastic; Biopdi; Afinko Polímeros; Wikipedia (somente artigos com fontes verificadas!).
Ultima atualização: 24 de Novembro de 2024.
Comentarios