Pra nós, basta olhar pra um objeto e dizer que ele possui plástico, borracha e ou metal em sua composição, mas não é bem assim que as coisas funcionam.
Plástico não é “tudo igual”, assim como a borracha e o metal também não são. É comum as pessoas classificarem a qualidade de um produto de acordo com essas terminologias, porém, devemos saber que há centenas de polímeros diferentes, que proporcionam milhares de combinações, isto é, compósitos, que permitem agregar características de diferentes materiais e criar produtos de alta qualidade. É o que ocorre com correias, que podem ser feitas de PA66-HNBR-GF-AF, de retentores que são feitos de PTFE ou FPM, de peças de motores e veículos feitas em PA66-GF ou PPGF, calços, coxins e batentes feitos em TPU, de dielétricos de capacitores feitos em PP, PE, PC e até polímeros semicondutores PPy e PEDT.
Mas para sabermos definir a qualidade de um produto, precisamos conhecer as combinações destes materiais, as qualidades e defeitos que cada um possui e a vantagem e desvantagem de utiliza-los. Também é necessário saber que há produtos iguais (que podem ser aplicados no mesmo sistema), todavia, feitos de materiais diferentes e com diferenças de preços gritantes, como é o caso de retentores. Um retentor de PTFE ou FPM possui uma durabilidade demasiadamente alta, entretanto, seus preços destoam das outras tecnologias mais defasadas, e essa falta de conhecimento do povo sobre as justificativas do preço alto fazem com que a maioria opte pelo mais barato achando que é “tudo a mesma coisa”.
Outra coisa fácil de se ver na população leiga e até entre profissionais desses ramos é que muitos não conhecem de fato o produto que estão utilizando (ou pelo menos insistem em utilizar termos errôneos). Um bom exemplo são as velhas juntas de vedação estáticas de cabeçotes de motores a combustão interna, que antigamente eram baseadas em Fibra de Amianto e que, pela legislação moderna, foram substituídas por Fibra de Vidro e ou Fibra de Aramida, porém, até hoje são conhecidas por todos como “juntas de amianto” ou “juntas de papelão de amianto”.
Nesta série de artigos, com a concatenação de informações selecionadas em vários sites, escritas por vários autores, trago a explicação resumida sobre Plásticos e Borrachas e exemplos de vários materiais compósitos que são utilizados amplamente pela indústria química, automobilística, eletrônica e diversas outras, porém, com enfoque na eletrônica e mecânica.
OBSERVAÇÃO: Este é um complemento do Capítulo 1, 2 e 3 sobre plásticos e borrachas.

Estado amorfo e semi-cristalino
Os polímeros em estado sólido possuem uma estrutura a qual depende do modo como suas cadeias moleculares estão arranjadas. Em função deste arranjo de cadeias, é possível definir duas classificações de estruturas, comumente chamadas de 'fase', sendo elas:
-> Fase amorfa: Que possui cadeias desordenadas;
-> Fase cristalina: Cadeias que se encontram em um arranjo tridimensional ordenado.
Portanto, tecnicamente não existe polímero totalmente cristalino, uma vez que mesmo uma fase cristalina apresenta pequenas regiões amorfas e, por isso, eles são classificados como semicristalinos ou amorfos.
Veja a imagem abaixo:
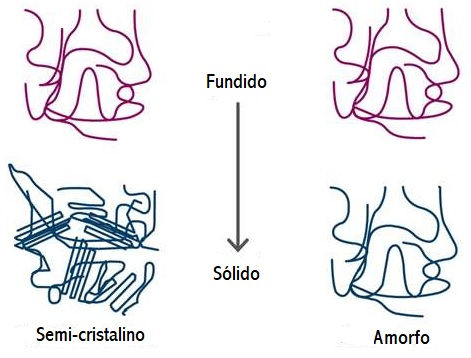
Imagem 1 - Polímeros amorfos e semi-cristalinos
Existem modelos que explicam a morfologia dos materiais poliméricos. Um dos mais antigos modelos é o de “Micela Franjada” e o atual é o de “Cadeias Dobradas”.
→ Micela Franjada: Os polímeros são constituídos por duas fases: pequenos cristalitos formados por segmentos moleculares de diferentes cadeias alinhados uns aos outros, dispersos em matriz amorfa. Porém, este modelo não explica a existência de monocristais poliméricos nem de esferulitos (estruturas formadas no processo de cristalização a partir de núcleos individuais que se desenvolvem radialmente).
→ Cadeias Dobradas: Apresenta os polímeros formados por lamelas que constituem os cristais. Nestes, as cadeias estão orientadas na direção normal à superfície das lamelas, dobradas de forma regular sobre si mesmas dentro do cristal.
São diversos fatores que afetam a cristalização, e em muitas situações práticas há mais de um fator contribuindo a cristalização ou não de um material. Entres os fatores que afetam a cristalização de um polímero estão:
→ Estrutura química do polímero (tamanho de cadeia, elementos químicos presentes, radicais químicos presentes, etc);
→ Presença de impurezas/aditivos: agentes nucleantes, cargas inorgânicas, pigmentos, contaminações, etc;
→ Condições de processamento do material: taxa de aquecimento e resfriamento do mesmo, posterior tratamento térmico;
→ Solicitações mecânicas.
Nem todos os polímeros amorfos são elastómeros. Alguns são plásticos, dependendo a classificação da temperatura de transição vítrea (Tg) definida como a temperatura acima da qual um polímero se torna mole e dúctil e abaixo da qual se torna duro e quebradiço (tipo vidro).
Podemos dizer, como regra geral só aplicável a polímeros amorfos, que um polímero amorfo que tenha uma Tg inferior à temperatura ambiente será um elastómero, enquanto que um polímero amorfo que tenha uma Tg superior à temperatura ambiente será um plástico.
Veja a imagem abaixo:

Complemento 1 - Os "crosslinks" são as ligações cruzadas feitas no processo de vulcanização do elastômero
A vulcanização é a quebra de ligações químicas do composto com a criação de pontes de enxofre (ou outro material apropriado) para reduzir a histerese do elastômero e melhorar sua consistência em ampla faixa de temperatura, já que a borracha 'crua' consegue ficar mole e pegajosa em dias mais quentes e dura e quebradiça em dias mais frios. Basicamente a vulcanização faz pontes que aumentam as ligações de cadeias de átomos, diferente do plástico, que possui cadeias ligadas por forças eletrostáticas.
CURIOSIDADE: O polietileno de baixa densidade (PELD) é um plástico e apresenta um estrutura polimérica amorfa por causa de pequenas “pontas soltas” (conhecidas como ramificações) que impedem das cadeias se aproximarem e organizarem, consequentemente há um espaço muito grande entre cada cadeia e a densidade do polímero diminui. Já o polietileno de alta densidade (PEHD) tem cadeias poliméricas quase totalmente livres de ramificações (sempre tem um ou outra para atrapalhar, mas em menor quantidade) e assim as cadeias podem se aproximar mais e o material fica mais denso.
CURIOSIDADE: O Poliéster pode ser tanto semi-cristalino quanto amorfo. Em objetos rígidos, como por exemplo garrafas PET ou carcaças de componentes automotivos feitas de PBT-GF é requerido Poliéster em estado semi-cristalino. Já em aplicações onde é necessário elasticidade, como por exemplo em malhas náuticas ou em TPE-Us, é utilizado o Poliéster amorfo.
Resumindo o que foi escrito até aqui, na estrutura amorfa, não existe qualquer ordenamento espacial dos átomos ou moléculas que constituem o material. Na estrutura cristalina existe um completo ordenamento espacial dos átomos e moléculas que constituem o material. Na estrutura semi-cristalina há regiões amorfas.
CURIOSIDADE: É num estado amorfo causado por aquecimento que o polímero com negro de fumo presente num PPTC (Fusível rearmável) reduz a passagem de corrente elétrica. Para saber mais sobre Fusíveis e PPTCs, CLIQUE AQUI!
CURIOSIDADE: O elastômero de policloropreno tem uma tendência acentuada para a cristalização. Este processo baseia-se na tendência à formação de cristais na macromolécula e é notável um endurecimento mais ou menos forte durante a conservação da borracha, da mistura crua (sem vulcanizar) ou do vulcanizado à temperatura ambiente (porém o efeito é mais intenso à baixas temperaturas).
A tendência à cristalização é maior na borracha ainda não trabalhada, podendo ser diminuída com a introdução de plastificantes ou outros materiais adequados. O endurecimento provocado pela cristalização só é uma vantagem para a fabricação de colas de contato / vedação, preferindo-se, neste caso, os graus com forte tendência à cristalização.
A cristalização é uma propriedade inerente às borrachas de policloropreno, embora uns tipos cristalizem mais rapidamente do que outros. À medida que a cristalização se desenvolve, ocorre uma pequena diminuição de volume, e a amostra sob tensão tende a relaxar e a alongar na direção da tensão.
A cristalização não ocorre em altas temperaturas pois as forças de orientação são dominadas pelo movimento molecular vigoroso. A cristalização é um fenômeno completamente reversível, bastando aquecer a amostra cristalizada a uma temperatura superior àquela á qual ocorreu a cristalização para que esta desapareça e o material volte a ter sua maciez e flexibilidade.
CURIOSIDADE: Quando um feixe de luz de determinada intensidade "IO" incide num material, uma parte deste feixe de luz atravessa o material. É a chamada intensidade transmitida "IT", porém uma parte do feixe luminoso é absorvida pelo material, sendo chamada de "IA" e uma outra parte do feixe é refletida, chamada de "IR".
Esta interação da luz com o material tem a ver com a sua estrutura ser amorfa, semi-cristalina ou cristalina, dando a característica de ser transparente, translúcido ou opaco, respectivamente.
Já que o assunto é luz, na continuação deste texto (Capítulo 5) será explicado mais sobre radiação UV e aditivos "anti-UV".

Vamos começar por algo que engloba tudo, e depois explicar suas partes...
Compósitos
A indústria atual requer cada vez mais materiais com características específicas, onde é necessário uma determinada rigidez dielétrica, uma determinada rigidez física, uma determinada flexibilidade e elasticidade, uma determinada absorção, distribuição e resistência ao calor e à luz, dentre vários outras propriedades... E foi assim que surgiram os compósitos!
Por exemplo, a fibra de vidro pura, embora de alta resistência, é demasiada 'macia' e só pode suportar forças de tração, não pode suportar esforços de compressão e não é facilmente moldado em uma forma geométrica fixa. Em resumo, é um corpo 'mole'. Se estes fios de fibra forem colados com uma resina sintética, eles podem se tornar uma variedade de produtos rígidos com uma forma geométrica fixa que pode resistir tanto a tensões de tração como de compressão (e, consequentemente, esforços de flexão, torção e corte). Isto constitui um compósito com matriz de plástico reforçado com fibra de vidro.
De forma simples, um compósito é a mistura de dois ou mais materiais diferentes que, com suas características combinadas, formam um novo material com propriedades superiores e específicas para determinadas aplicações.
Agora precisamos conhecer a estrutura básica de um compósito:
Um polímero pode ser um aglutinante. Um aglutinante é uma cola, um agente de ligação, que pode ligar fibras, pó de enchimento e etc. No caso de uma peça de um veículo feita em PA66-GF35, temos a Poliamida em forma de resina sendo o aglutinante para material de reforço, que no caso é os 35% de lã de vidro adicionados, fazendo uma peça do tipo PRFV (Plástico Reforçado com Fibra de Vidro).
O mesmo ocorre com uma peça feita em PP-T40, onde o aglutinante Polipropileno é reforçado com 40% de Talco para gerar uma peça moldada com determinado grau de rigidez física, rigidez dielétrica...
Sendo o aglutinante uma 'cola', aquelas gambiarras que eu e você fazemos utilizando lã de algodão com Super Bonder (etil-cianoacrilato com aditivações) seguem a mesma lógica. O Super Bonder é o aglutinante que fará a ligação entre as fibras de algodão, tornando-se uma peça resistente e sólida.
Partindo desse raciocínio, tanto a peça em PA66-GF35, quanto a de PP-T40, quanto a gambiarra de Super bonder e Algodão são chamados de "composites" (compósitos).
Observe os exemplos:|
→ No PA66-GF35, a resina de Poliamida é a matriz e a lã de vidro é o reforço (também chamada de 'fase dispersa').
→ No PP-T40, a resina de Polipropileno é a matriz e o Talco é o reforço.
→ Na gambiarra, o Super Bonder é a matriz e o Algodão é o reforço.
→ Numa correia feita em PA66 / EPDM, a resina EPDM é a matriz e a malha de fibra de poliamida é o reforço;
→ Numa correia dentada de HNBR / PA66 / GF, a resina de borracha HNBR é a matriz e a malha de fibra de poliamida somada com a malha de fibra de vidro são os reforços.
→ Numa peça feita em PP+EPDM-MD20, as resinas de Polipropileno e borracha EPDM formam um TPE-O ou TPE-V, que é a matriz. O MD é o reforço ou material de enchimento.
Você verá mais sobre retardantes de chama e fillers (FR e MD) se continuar lendo este capítulo e o próximo (Capítulo 5)...
Resina
Resina sintética é uma substância viscosa produzida em laboratório e que pode ser moldada (plástico) e virar um sólido.
Ou seja, de forma simples, podemos definir a resina como um 'líquido' que pode ser moldado e dar origem a um objeto sólido. E se tratando de termoplásticos, o objeto pode ser derretido e voltar ao estado de resina, sendo moldada novamente para dar origem a outro produto.
Veja mais sobre termoplásticos e termorígidos no Capítulo 2 desta série!
Existem também as resinas naturais, isto é, as secreções retiradas da natureza, como por exemplo o Latex, utilizado na produção de borracha natural.
Sendo assim, uma resina também pode ser moldada em finos fios, que são chamados de "Fibras".
Mas o que são fibras?
As fibras são materiais muito finos e alongados, como filamentos, que podem ser contínuos ou cortados. Podem ser de comprimento limitado (fibras em sentido estrito) ou praticamente indefinido (filamentos). Podem estar isoladas ou agrupadas em blocos. As fibras usadas na manufatura são classificadas conforme a sua origem, que pode ser natural, artificial ou sintética.
Fibras Naturais
São as fibras retiradas prontas da natureza, podendo ser de origem vegetal ou animal:
-> Nas fibras de origem vegetal temos as chamadas “fibras semente”, sendo as mais comuns o Algodão (CO), o Linho (CL), Rami (CR) e a Juta (CJ), Cana-de-Açucar (bagaço, CM) todas a base de celulose;
-> Nas fibras de origem animal, temos a Seda (SK ou S), Mohair (WM), Caxemira (WK) e a Angorá (WA).
Por algum tempo, a Ford Motor Company do Brasil investiu na substuição de fibra de vidro por fibras vegetais, tal como Sisal, Juta e bagaço de Cana em algumas peças plásticas
Da virada do século pra cá, vários fabricantes investiram na pesquisa sobre uso de fibras vegetais misturadas com polímeros, bem como processos de produção envolvendo tais materiais para se reduzir a dependência do vidro e de matéria-prima virgem oriunda do petróleo, entretanto, até hoje tais compósitos se restringem a partes do habitáculo, nada relacionado ao sistema mecânico e elétrico / eletrônico dos veículos.

Complemento 2 - O uso de fibras vegetais na indústria automobilística
Caso queira saber mais detalhes sobre fibras vegetais e sobre o complemento acima, acesse o seguinte PDF:
Caso queira saber mais sobre o projeto da Ford de usar fibras vegetais em compósitos, leia a patente (em inglês):
Este é apenas um dos vários documentos relacionados ao Ford EcoProject. Seguimos com o próximo tópico...
Fibras Artificiais
Fibras artificiais: São produzidas pelo Ser Humano, porém, utilizando como matéria-prima base produtos da natureza, como por exemplo a celulose. As mais comumente utilizadas são a Viscose (CV), o Acetato (CA), o Lyocel e o Modal.
A celulose é um grande exemplo de polímero produzido pela natureza, que quando extraído de plantas e industrializado, pode gerar fibras das mais diversas medidas, que serão usadas na indústria de papel.
Pode ser uma folha de papel sulfite ou então um filtro de café, a fibra de celulose está lá. Para termos uma noção de sua estrutura, separei algumas imagens de microscópio de filtros utilizados na indústria automobilística:
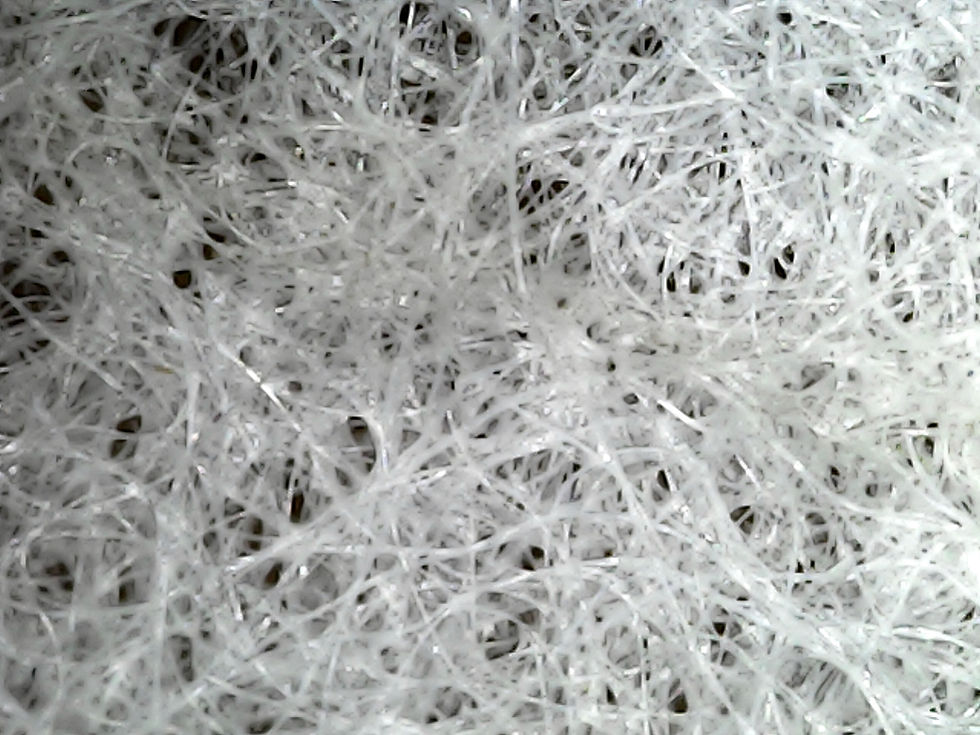
Imagem 2 - Filtro de ar do habitáculo (sem carvão ativado) da marca Mahle / Metal Leve
Enquanto o filtro de cabine da imagem acima têm fios mais grossos e poros maiores, o filtro de gasolina da imagem abaixo é bem mais denso:

Imagem 3 - Filtro de Gasolina da marca TecFil
Para efeito de comparação, um filtro de café, da marca Brigitta:

Imagem 4 - Filtro de fibra de celulose para coar café
Note que a gramatura, isto é, a densidade do papel (medida em g/m³), muda de acordo com a aplicação.
Agora, veja imagens de fibras de madeira (Wood Fiber) aglutinadas com Polifenol (PF) que compõem os forros de porta de alguns automóveis:

Imagem 5 - Fibras de madeira ligadas por resina fenólica e utilizadas no acabamento interno de alguns automóveis
Fibras Sintéticas (ou Orgânicas)
Fibras sintéticas ou orgânicas: São fibras produzidas pelo Ser Humano usando como matéria-prima resinas sintéticas obtidas a partir de compostos retirados do petróleo ou outros materiais, tais como amônia. As mais conhecidas são o Poliéster (saturado é "SP" e insaturado é "UP"), a Poliamida (PA), o Acrílico (PMMA), o Polipropileno (PP) e o Poliuretano (PU), além das Aramidas (PPTA ou PMIA).
Um bom exemplo de material que mistura fibras de PE, PA, PP e PET é o carpete:

Imagem 6 - Este é o forro do capô de um Ford Focus MK1. Note que o carpete nada mais é que um denso feltro de fibras sintéticas
OBSERVAÇÃO: A face preta é uma impregnação de partículas de borracha (tal como o EPDM, comum nestas aplicações automotivas) cuja função é facilitar a conformação do feltro fibroso para que ele admita um formato específico.
Já que estamos falando sobre fibras, é relevante saber alguns detalhes sobre a fibra de vidro - outro tipo de fibra sintética - , pois ela é muito utilizada para reforço estrutural em componentes de plástico.
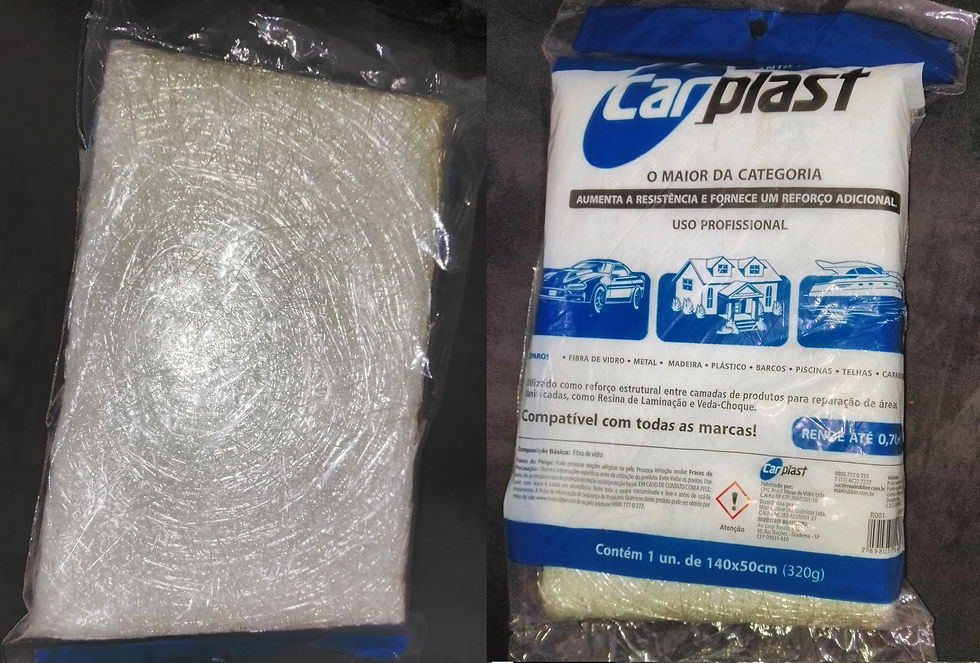
Imagem 7 - Manta de fibra de vidro para remendos em auto-peças e outros bens de consumo encontrada em lojas de ferramentas
Para conhecer mais sobre a composição do vidro, CLIQUE AQUI! leia o artigo dedicado ao assunto.
Para gerar Fibra de Vidro (Fiber Glass – Abreviado por GF), os óxidos que o compõem são aquecidos até ficar em estado líquido (cerca de 1600 °C). Este líquido é submetido ao resfriamento sob alta velocidade, onde o controle cinético e térmico favorece a obtenção de fios de tamanhos e diâmetros desejáveis ao atravessar uma espécie de “grade” de Platina, através de furos extremamente finos que são reguláveis e podem produzir diversas espessuras de fios. Esse processo cria fios de vidro tão finos que são melhor medidos em mícrons (uma unidade de comprimento que equivale a um milionésimo de metro). A junção de milhares destes fios forma a chamada “Lã de Vidro” (em aparência é semelhante a Lã de Algodão).
Na indústria química, a Lã de Vidro pode ser adicionada a um aglutinante e formar uma estrutura super resistente denominada PRFV (Plástico Reforçado com Fibra de Vidro).
É o que ocorre com componentes feitos em PA66-GF30, uma mistura de Poliamida com 30% de Fibra de Vidro, ou então PPGF35, uma mistura de Polipropileno com 35% de Fibra de Vidro.
No caso de correias, o compósito pode ser formado por uma malha em Fibra de Vidro (GF), que em paralelo com uma malha de Poliamida (PA66), ambas incorporadas numa matriz de Borracha Hidronitrílica (HNBR), formam uma cinta de alta resistência capaz de sincronizar e transmitir força e movimento entre duas ou mais polias ou engrenagens.

Imagem 8 - Uma correia dentada 6K288-BA feita em HNBR-GF-PA66 aplicada em um motor FoMoCo (Ford Motor Company).
Existem casos onde uma manta de lã de vidro é colocada em uma fôrma e impregnada com resina plástica, tal como Poliepóxido ou Poliéster Insaturado. Ao curar, forma uma peça rígida de "fibra de vidro", levando este nome por ter predominantemente material fibroso e o restante de resina aglutinante.

Imagem 9 - Esta imagem é da moldura de fibra de vidro que envolve as lanternas de um semi-reboque Triel-HT. Diferente de uma peça em PRFV, uma quebra torna exposto a predominância da fibra de vidro na estrutura
CURIOSIDADE: Para finalizar, mais um exemplo de fibra que é comum em nosso cotidiano: A Fibra de Aço!
Popularmente conhecida como "palha de aço", "lã de aço" ou simplesmente pelo nome comercial "Bombril", a fibra de aço é um outro bom exemplo de fibra. Atualmente ela é utilizada em CRFA (Concreto Reforçado com Fibra de Aço) substituindo as estruturas de ferro amarrado utilizadas para reforçar as construções.
Pó
Os materiais termorígidos, como por exemplo baquelite (polifenol) e o Poliepóxido podem ser moídos e utilizados como pó de enchimento para dar volume em novas resinas, já que estes materiais não derretem tal como ocorre com os termoplásticos, limitando as formas de reciclagem. Este é apenas um exemplo de pó de enchimento.
Para melhorar as características de um material, as vezes é necessária a adição de outro(s) componente(s) químico(s). É aí que entram as fibras e os pós de enchimento. As fibras já foram explicadas no tópico anterior, e os pós ganham espaço aqui.
Excluindo os termorígidos moídos citados anteriormente, podemos separar os pós de enchimento para resinas poliméricas em duas classes:
→ Cargas brancas: Aqui entram o Talco, esferas ou pó de vidro; Carbonato de Cálcio, Óxido de Zinco, entre outros.
CURIOSIDADE: A Fibra de vidro traz realmente uma resistência estrutural maior para componentes de plástico, como é o caso de um tubo plástico do sistema de arrefecimento de um motor, que precisa trabalhar com altas pressões e temperaturas, e uma resina plástica reforçada com lã de vidro traz mais segurança e durabilidade ao componente. Todavia, em alguns componentes há a necessidade de uma maior estabilidade dimensional. Este reforço é basicamente composto de esferas de vidro, ou a grosso modo, vidro em pó.
O GB, sigla para "Glass Bead" (vidro em esferas) pode ser utilizado em sistemas eletrônicos, como por exemplo placa de soquetes de relés e fusíveis, onde a corrente elétrica é alta bem como a geração de calor, consequentemente, havendo a necessidade de uma maior homogeneidade na estrutura do compósito, uma alta rigidez dielétrica e resistência para altas temperaturas, tornando o pó de vidro mais vantajoso que a lã. Veja o gráfico abaixo com algumas resinas plásticas e vantagens e desvantagens do uso de GF e GB:

Infográfico 1 - Algumas resinas plásticas e o uso de GF e GB
→ Cargas negras: Aqui pode ser dado como exemplo o Negro de Fumo, Carbono Grafênico e o Grafite.
CURIOSIDADE: É interessante dissertar um pouco sobre o Negro de Fumo, um dos maiores aditivos utilizados na indústria química mundial.
O Negro de Fumo só começou a ser fabricado em escala industrial a partir de 1870, para atender às necessidades da indústria de tintas. A descoberta das propriedades reforçantes deste material em polímeros, ocorrida nos primeiros anos do século XX elevou este produto à condição atual de carga mais importante para esta indústria, sendo indispensável em muitas aplicações.
Existem vários tipos de Negro de Fumo, e todos eles se enquadram nas seguintes classes principais, que possuem tais nomes pois se referem ao método de obtenção:
-> Negro de Lamparina (Lamp Black);
-> Negro de Canal (Channel Black);
-> Negro Térmico (Thermal Black);
-> Negro de Acetileno (Acetylene Black);
-> Negro de Fornalha (Furnace Black).
O negro de fornalha predomina de forma quase absoluta, constituindo mais de 99% do total de negros de fumo produzidos no mundo, devido aos custos mais reduzidos e por cobrir a grande maioria das aplicações existentes. Os outros processos são utilizados essencialmente para obter as especialidades, requeridas em aplicações muito específicas, como por exemplo nos PPTCs, fusíveis rearmáveis que utilizam um polímero com características isolantes misturado com um negro de acetileno, que dentre todas as classes é a que mais tem negros de carbono com características condutivas que se assemelham ao Grafite.

Imagem 10 - As pilhas Super Hyper da Panasonic usam um pino coletor de corrente feito de Negro de Acetileno
As pilhas e baterias ácidas ou alcalinas, quando não possuem um pino de Grafite fazem uso de um composto de Negro de Acetileno. De qualquer maneira, elas são genericamente e vulgarmente chamadas de "pilha zinco-carvão", ou "pilha de zinco-carbono" ou "bateria zinco-carvão".
Para saber mais sobre acumuladores de energia, comece CLICANDO AQUI!
O negro de fumo também ajuda a dissipar o calor da banda de rodagem e da área de contato do pneu com o solo, reduzindo os danos térmicos e aumentando a vida útil. Praticamente todos os produtos de borracha onde as propriedades de tração e desgaste por atrito são levadas em conta usam algum tipo de negro de fumo, e também por isso são de cor preta (é um dos mais comuns e baratos pigmentos do mundo). Cerca de 20% da produção mundial vai para correias, mangueiras e outros produtos de borracha que não sejam pneus.
Mais adiante neste texto, você verá que o negro de Carbono também é utilizado como aditivo anti-UV em alguns materiais.
Além do tipo utilizado (Acetileno, Lamparina, Canal, Térmico e etc.), vários fatores influenciam na condutividade elétrica, distribuição de calor e resistência física proporcionada pelo negro de carbono:
1. Geometria e composição de negro de Carbono:
-> Tamanho da partícula;
-> Formato da partícula;
-> Porosidade;
-> Teor de matérias orgânicas voláteis e não voláteis.
2. Quantidade de negro de Carbono no composto;
3. Grau de dispersão do negro de fumo no composto:
-> Tipo de processamento;
-> Tempo de processamento;
-> Temperatura de processamento.
Para finalizar este conteúdo, é interessante saber sobre a composição química das partículas de negro de Carbono. Apresentam-se a seguir, a composição básica de negros de carbono da classe fornalha e canal, embora dentro de cada uma dessas classes (ou grupos) se possam encontrar tipos de composição química diferenciados:

Tabela 1 - Do que é composto o negro de Carbono
Embora os negros de fumo sejam constituídos essencialmente por Carbono, eles apresentam outros elementos, em pequenas quantidades, sendo normalmente Oxigênio, Hidrogênio e Enxofre. Muitas das propriedades dos negros de Carbono estão correlacionadas com as quantidades relativas destes elementos dominantes. O enxofre está ligado aos átomos de Carbono e não interfere no processo de vulcanização. O Nitrogênio pode existir também, embora em muito pequena quantidade. Cinzas, humidade, gases oclusos, matérias orgânicas voláteis e não voláteis estão também usualmente presentes.

Depois de todo este resumo sobre diversos materiais utilizados na indústria - incluindo o Capítulo 1, 2 e 3 - podemos concluir que:
→ Fibras são fios muito finos e flexíveis, que em grandes quantidades formam lãs (tipo lã de vidro e lã de algodão);
→ Plásticos podem ter qualquer forma, bastando molda-los com calor e pressão;
→ Plásticos são resinas sintéticas que podem admitir a forma de fibra;
→ Resinas sintéticas são feitas de monômeros, que formam os polímeros.
→ Borrachas são resinas que podem ser de origem natural ou sintética;
→ Borrachas, independente da origem, são elásticas, ou seja, elastômeros;
→ Tanto a borracha sintética quanto o plástico são resinas;
→ Tanto a borracha quanto o plástico são feitos de polímeros. O que difere uma borracha de um plástico é seu comportamento mecânico, ou seja, a elasticidade.
→ Elastômeros são geralmente termofixos. Os TPEs são elastômeros termoplásticos;
→ Plásticos podem ser divididos entre termofixos e termoplásticos;
→ Um compósito é a mistura de dois ou mais materiais diferentes para se criar um terceiro com características melhores / especificas.
Para fechar o raciocínio, nos plásticos as moléculas poliméricas são mantidas unidas apenas pelas forças eletrostáticas, enquanto nas borrachas há um processo chamado vulcanização que liga as moléculas entre si por meio de ligações químicas (geralmente pontes de enxofre, porém a vulcanização sem enxofre também pode ser feita - podem ser utilizados óxidos metálicos, peróxidos orgânicos ou até resina de poliepóxido), o que faz com que a estrutura polimérica seja um pouco flexível, admitindo que a borracha se deforme e acumule energia, mas quando a força cessa essa energia é liberada e as moléculas retornam às suas posições.
Os plásticos, quando submetidos à uma força, se deformam de forma permanente (ou plástica) e a energia gasta na deformação se dissipa como calor, não havendo nada para recuperar a forma original do corpo quando a força cessa.
A borracha tem um estrutura química amorfa e só admite um baixo grau de cristalização quando tensionada. Já o plástico geralmente é semi-cristalino, com cadeias de átomos organizadas em meio a regiões amorfas. Um exemplo de exceção é o Polietileno, que pode ser plástico amorfo quando PELD ou semi-cristalino quando PEHD.

Para saber mais sobre retardantes de chama, materiais de enchimento, aditivos anti-UV, propriedades elétricas e mecânicas dos materiais polímericos, bem como nomenclaturas e formas de identificação, leia o Capítulo 5, que é a continuação deste texto. Para isso, basta CLICAR AQUI!
Para conhecer mais profundamente um tipo de compósito 'feijão com arroz' da indústria eletrônica e automobilística há uns 40 anos, CLIQUE AQUI!
Agora sim, depois de tanto ler sobre fibras, borrachas e plásticos, e entender suas diferenças, misturas, aplicações, deve ter ficado claro que estes materiais são a base de quase tudo o que estão ao nosso redor e que eles são fundamentais para nossa sociedade.
Caso tenha ficado algum "ponto solto", alguma discordância, erros de digitação e caso esteja faltando alguma coisa, ou você queira trazer sugestões ao blog, entre em contato pelo hardwarecentrallr@gmail.com.
Texto: Leonardo Ritter.
Imagens, gráficos e desenhos: Google Imagens
Fontes: Rubberpedia (Manuel Morato Gomes); Mundo Educação (Jennifer Fogaça); Brasil Escola (Jennifer Fogaça); SABÓ; ANIP (Associação Nacional da Indústria de Pneumáticos); Vedamotors; Fricwel; Fras Le; Akroplastic; Wikipedia (somente artigos com fontes verificadas!).
Ultima atualização: 02 de Novembro de 2024.
Comments