Mais um artigo da série sobre eletrônica, desta vez sobre o capacitor de cerâmica!

Imagem 1
Caso você não tenha lido a introdução sobre capacitores, isto é, os Capítulos 2.0 e 2.1, aconselho você a ler para que entenda melhor os termos utilizados neste texto e o funcionamento de capacitores
Para ler o Capítulo 2.0, basta CLICAR AQUI para acessar!
Para ler o Capítulo 2.1, basta CLICAR AQUI para acessar!
Vamos começar com uma breve história dos capacitores de cerâmica...
A origem desta família de componentes está diretamente relacionada com a disponibilidade baixa do mineral Mica no início do século passado.
Na década de 1920, na Alemanha, a escassez de Mica e a experiência com Porcelana - uma classe especial de cerâmica - levaram aos primeiros capacitores usando cerâmica como dielétrico.
O Dióxido de Titânio paraelétrico (Também conhecido como Rutilo) foi usado como o primeiro dielétrico cerâmico, pois tinha uma linearidade entre temperatura e capacitância. Já em 1926, esses capacitores de cerâmica foram produzidos em pequenas quantidades, que aumentaram na década de 1940.
O estilo dessas primeiras cerâmicas era um disco com metalização em ambos os lados em contato com fios estanhados. Esse estilo foi usado extensivamente em equipamentos valvulados de 1930 a 1950.
Mas esse dielétrico paraelétrico tinha permissividade relativamente baixa, de modo que apenas pequenos valores de capacitância podiam ser implementados. A expansão do mercado de rádios nas décadas de 1930 e 1940 criou uma demanda por valores de capacitância mais altos, mas abaixo dos capacitores eletrolíticos para aplicações de desacoplamento de Alta Frequência.
Descoberto em 1921, o Titanato de Bário, material cerâmico ferroelétrico, com permissividade na faixa de 1.000 - cerca de dez vezes maior do que o Dióxido de Titânio ou Mica - começou a desempenhar um papel muito maior nas aplicações eletrônicas.
Todavia, apesar da permissividade mais alta, os parâmetros elétricos de algumas aplicações impediram a expansão do Titanato de Bário, que só poderia substituir a Mica em sistemas onde a estabilidade era menos importante. Apesar de tudo isso, as dimensões menores em comparação com os capacitores de Mica, menores custos de produção e independência da disponibilidade do mineral filossilicato aceleraram a aceitação dos novos capacitores cerâmicos.
O rápido crescimento da indústria de radiodifusão após a Segunda Guerra Mundial levou a uma compreensão mais profunda da cristalografia, das transições de fase e da otimização química e mecânica dos materiais cerâmicos. Por meio da complexa mistura de diferentes materiais, as propriedades elétricas dos capacitores de cerâmica podem ser ajustadas com precisão.
Para distinguir as propriedades elétricas dos capacitores de cerâmica, a padronização definiu várias classes de aplicação diferentes (Classe 1, Classe 2 e Classe 3). É notável que o desenvolvimento separado durante a guerra e no período posterior nos EUA e na Europa levou a diferentes definições dessas classes (EIA e IEC), e apenas recentemente (desde 2010) houve uma harmonização mundial com a padronização IEC.
O estilo inicial do capacitor (disco de cerâmica) poderia ser produzido mais barato do que os capacitores de tubo de cerâmica comuns nas décadas de 1950 e 1970. Uma empresa americana, na época do programa Apollo, lançado em 1961, foi pioneira no empilhamento de vários discos para criar um bloco monolítico. Este "capacitor de cerâmica multicamada" (MLCC) era compacto e oferecia alta capacitância.
Os MLCCs expandiram a gama de aplicações para aquelas que requerem valores de capacitância maiores em espaços menores. Esses componentes foram a força motriz por trás da implementação massiva da tecnologia de montagem em superfície (SMD) na década de 1980.
Outra grande evolução foi em 1993, quando a TDK Corporation conseguiu substituir eletrodos (armaduras do capacitor) de Paládio por eletrodos de Níquel, reduzindo significativamente os custos de produção e permitindo a produção em massa de MLCCs. A Prata também é comum para este fim, apesar de ser mais cara.

Valores mais altos de capacitância para capacitores de cerâmica podem ser obtidos usando misturas de materiais ferroelétricos como Titanato de Bário com óxidos específicos (tipo minerais silicatos ou até mesmo Alumina, a cerâmica técnica mais comum). Esses materiais dielétricos têm permissividades muito maiores, mas ao mesmo tempo seus valores de capacitância são mais ou menos não lineares na faixa de temperatura e as perdas em altas frequências são muito maiores.
Enfim, as diferentes características elétricas dos capacitores cerâmicos, que circundam sempre nos três itens principais (temperatura, tensão e capacitância) exigem agrupá-los em "classes de aplicação". Em 2013, dois conjuntos de padrões estavam em uso, um da International Electrotechnical Commission (IEC) e outro da agora extinta Electronic Industries Alliance (EIA).
Classe 1
Os cerâmicos Classe 1 são componentes com bastante linearidade entre tensão, capacitância e temperatura. Eles oferecem a mais estável tensão, temperatura e, até certo ponto, frequência. Eles têm as perdas mais baixas e, portanto, são especialmente adequados para aplicações de circuito ressonante onde a estabilidade é essencial ou onde um coeficiente de temperatura precisamente definido é necessário.
Os materiais básicos dos capacitores de cerâmica desta classe são compostos de uma mistura de grânulos finamente moídos de materiais paraelétricos, como o dióxido de titânio (TiO2), modificado por aditivos como Zinco, Zircônio, Nióbio, Magnésio, Tântalo, Cobalto e Estrôncio, que são necessários para atingir as características lineares desejadas do capacitor.
Estes capacitores apresentam a menor eficiência volumétrica dentre os cerâmicos. Este é o resultado da permissividade relativamente baixa (6 a 200) dos materiais paraelétricos. Portanto, possuem valores de capacitância inferiores.

Tabela 1 - Materiais cerâmicos mais comuns utilizados na Classe 1
Os capacitores desta classe não sofrem nenhum processo significativo de envelhecimento e o valor da capacitância é quase independente da tensão aplicada. Essas características permitem aplicações para filtros de alto Q, em circuitos ressonantes e osciladores (por exemplo, em circuitos PLL).
O padrão EIA RS-198 codifica os capacitores de cerâmica Classe 1 com um código de três caracteres que indica o coeficiente de temperatura.
-> A primeira letra dá o algarismo significativo da mudança na capacitância ao longo da temperatura (coeficiente de temperatura α) em ppm/K.
-> O segundo caractere fornece o multiplicador do coeficiente de temperatura.
-> A terceira letra fornece a tolerância máxima em ppm/K.
Todas as classificações são de 25 a 85 °C. Observe a tabela:
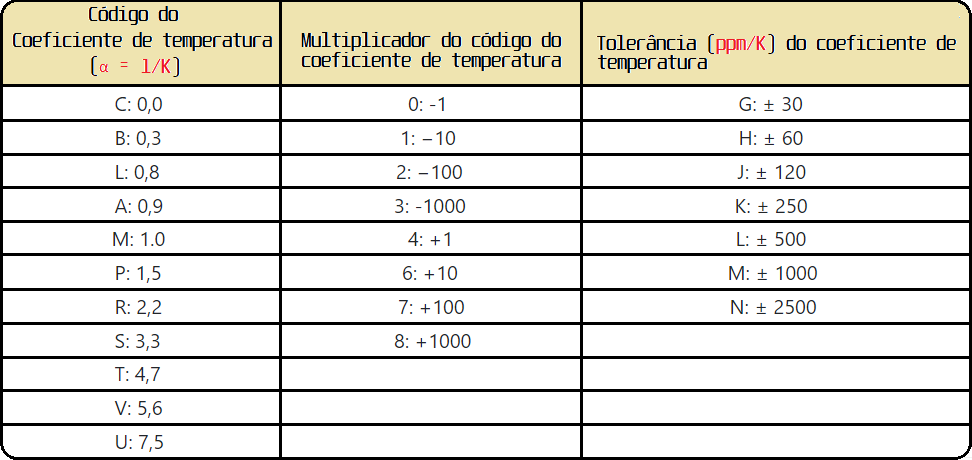
Tabela 2 - Códigos alfabéticos do coef. de temperatura α de capacitores de cerâmica Classe 1 (referindo-se a EIA-RS-198)
Além do código EIA, o coeficiente de temperatura dos capacitores de cerâmica de Classe 1 é comumente expresso em códigos como por exemplo "NP0" e "N220". Na norma IEC / EN 60384-8 / 21, o coeficiente de temperatura e a tolerância são substituídos por um código de letras de dois dígitos, no qual o código EIA correspondente é adicionado. Veja a tabela:
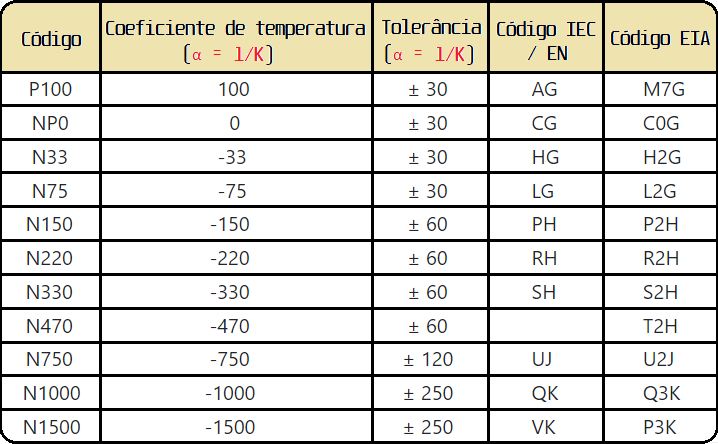
Tabela 3 - Códigos "Negativo / Positivo" para representar o coeficiente de temperatura
Por exemplo, um capacitor "NP0" com código EIA "C0G" terá desvio 0, com tolerância de ± 30 ppm/K, enquanto um "N1500" com código "P3K" terá desvio de −1500 ppm/K, com uma tolerância máxima de ± 250 ppm/°C.
Capacitores com o código NP0 (ou um risco preto na parte de cima do disco) significa um coeficiente de temperatura nulo ou compensado.
Observe que os códigos IEC e EIA são para capacitores industriais e diferentes dos códigos de capacitores militares.
Especialmente capacitores NP0 / CG / C0G com α ± 0 e tolerância 30 ppm são de grande interesse para a indústria. Esses capacitores têm uma variação de capacitância de ± 0,54% na faixa de temperatura de -55 a +125 °C. Isso permite uma resposta de frequência precisa em uma ampla faixa de temperatura (em, por exemplo, circuitos ressonantes). Os capacitores Classe 1 exibem tolerâncias muito pequenas da capacitância nominal.
Classe 2
Os cerâmicos de Classe 2 têm um dielétrico com alta permissividade e, portanto, uma melhor eficiência volumétrica do que os capacitores de Classe 1 (são significativamente menores do que os dispositivos de classe 1 na mesma capacitância e tensão nominais), mas com menor precisão e estabilidade.
Capacitores de Classe 2 são feitos de materiais ferroelétricos, como o Titanato de Bário (BaTiO3) e aditivos adequados, tais como:
-> Aluminossilicato;
-> Talco (Silicato de Magnésio);
-> Alumina (Óxido de Alumínio).
Essas cerâmicas têm permissividade alta a muito alta (200 a 14.000), o que depende da intensidade do campo elétrico, portanto, o valor da capacitância é não linear, isto é, depende da temperatura e da tensão aplicada. Além do mais, os cerâmicos de Classe 2 envelhecem com o tempo.
Eles são adequados para aplicações de bypass, acoplamento e desacoplamento ou para circuitos de discriminação de frequência, onde baixas perdas e alta estabilidade de capacitância são menos importantes.
Os capacitores de Classe 2 são rotulados de acordo com a mudança de capacitância em relação a temperatura. A classificação mais usada é baseada no padrão EIA RS-198 e usa um código de três dígitos.
-> O primeiro caractere é uma letra que indica a temperatura de operação miníma;
-> O segundo fornece a temperatura operacional máxima;
-> e o caractere final fornece a mudança de capacitância nessa faixa de temperatura.
Observe a tabela:
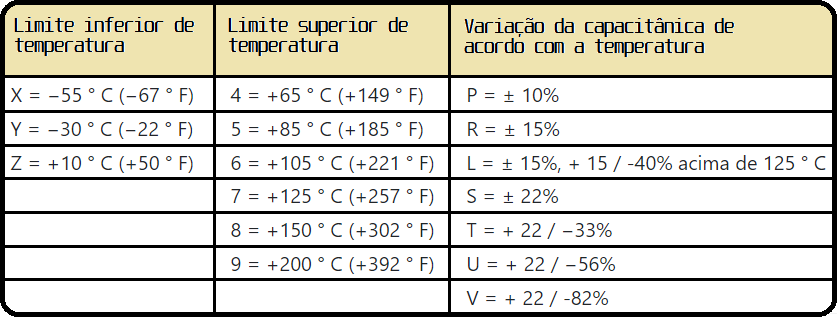
Tabela 4 - Sistema de código definido pela EIA RS-198 para cerâmicos de Classe 2
Por exemplo, um capacitor Z5U operará de +10 °C a +85 °C com uma mudança de capacitância de no máximo + 22% a -56%. Um capacitor X7R operará de −55 °C a +125 °C com uma mudança de capacitância de no máximo ± 15%.
Vale lembrar que alguns modelos de capacitores cerâmicos, principalmente os em formato de disco, as vezes vem com o valor de tensão impresso. Normalmente, os Classe 2 não informam os valores de tensão, pois suportam um valor bem alto e com boa tolerância.
Algumas codificações comumente usadas são listadas abaixo:
-> X8R (−55 / +150 °C, ΔC/C 0 = ± 15%),
-> X7R (−55 / +125 °C, ΔC/C 0 = ± 15%),
-> X6R (−55 / +105 °C, ΔC/C 0 = ± 15%),
-> X5R (−55 / +85 °C, ΔC/C 0 = ± 15%),
-> X7S (−55 / +125 °C, ΔC/C 0 = ± 22%),
-> Z5U (+10 / +85 °C, ΔC/C 0 = + 22 / −56%),
-> Y5V (−30 / +85 °C, ΔC/C 0 = + 22 / −82%),
OBSERVAÇÃO: O termo "ΔC/C" significa a variação da capacitância em relação a temperatura!
O padrão IEC / EN 60384 -9/22 usa outro código de dois dígitos que, ao momento, não será apresentado aqui.
Como os capacitores de Classe 2 têm menor precisão e estabilidade de capacitância, eles exigem maior tolerância.
Para os tipos militares, os dielétricos de Classe 2 especificam a característica de temperatura (TC), mas não a característica de temperatura-tensão (TVC). Semelhante ao X7R, o tipo militar "BX" não pode variar mais de 15% em relação à temperatura e, além disso, deve permanecer dentro de +15% / -25% na tensão nominal máxima. O tipo BR tem um limite de TVC de +15% / -40%.
Classe 3
A Classe 3 traz componentes com permissividade muito alta, até 50.000 e, portanto, uma melhor eficiência volumétrica do que os capacitores de Classe 2. Todavia, esses capacitores têm características elétricas piores, incluindo menor precisão e estabilidade. O dielétrico é caracterizado por uma mudança não linear muito alta de capacitância em relação a temperatura. O valor da capacitância também depende da tensão aplicada. Da mesma forma, eles têm perdas muito altas e envelhecem ainda mais ao longo do tempo.
Capacitores de cerâmica de Classe 3, conhecidos também como "capacitores de barreira de potencial" são feitos à base de materiais ferroelétricos dopados, como o CCTO. Como há mais dificuldade - inviabilidade financeira - de construir capacitores multicamadas com este material, apenas os tipos de camada única são oferecidos no mercado.
Com o aprimoramento dessa tecnologia de cerâmica em meados da década de 1980, esta classe tornou-se disponível em valores de até 100 µF e, naquela época, parecia que ia substituir os capacitores eletrolíticos menores, coisa que não ocorreu. A partir de 2013, estes componentes foram considerados obsoletos, pois as cerâmicas multicamadas Classe 2 modernas podem oferecer capacitâncias mais altas e melhor desempenho em um pacote mais compacto. Como consequência, esses capacitores não são mais padronizados pela IEC.

Os capacitores cerâmicos possuem capacitância na faixa dos Pico Farads (pF) e Nano Farads (nF) e podem trabalhar em circuitos de alta ou baixa frequência (de acordo com sua classe). Estes componentes também não possuem polaridade, ou seja, podem ser posicionados de qualquer maneira entre os polos positivo e negativo do circuito, já que não há diferença de material ou tamanho nos dois eletrodos.
A composição do dielétrico
As cerâmicas, feitas a partir de Óxidos metálicos, Boretos, Carbetos ou Nitretos são caracterizadas por passar por um tratamento térmico específico após sua moldagem. No caso dos capacitores, o composto cerâmico em pó (com diversos valores de tamanho de grão, de acordo com o projeto do componente) é moldado em finas folhas ou discos através de sinterização (moldagem por alta pressão e colar), posteriormente passando por tratamento térmico (também em temperaturas especificas de cada projeto) para atingir rigidez dielétrica e outras características elétricas desejadas.
Para entender melhor a estrutura dos capacitores cerâmicos MLCC e dos outros formatos também, é necessário compreender que o processo de queima só é feito após a conformação do material dielétrico e da colocação dos eletrodos. Ou seja, os componentes já estão definidos ao entrarem no forno. Veja mais sobre o processo de fabricação dos capacitores MLCC no tópico "Complemento".
Para entender melhor como uma cerâmica é produzida (a sinterização), recomendo a leitura do artigo dedicado ao assunto publicado pelo HC. Para acessa-lo CLIQUE AQUI!
Um dos compostos mais comuns no mercado é o pó cerâmico de Titanato de Bário (BaTiO), mas também há capacitores com cerâmica a base de Óxido de Zinco e Tântalo (ZnTaO), Óxido de Magnésio e Nióbio (MgNbO), além do primordial Dióxido de Titânio, entre outros. Para ver a lista de materiais mais comuns, retorne para a TABELA 1.
Minerais silicatos e Alumina podem ser utilizados como aditivo no Titanato de Bário para alguns capacitores cerâmicos. Você leu mais sobre isso no tópico "Classificação".
No caso dos capacitores de camada de barreira, um dos materiais que podem ser utilizados é a cerâmica dopada CCTO, sigla para CaCu3Ti4BaO12.
Ao sair do forno, as pastilhas são inspecionadas e vão para uma outra máquina que vaporiza Prata OU Níquel nas duas faces, formando assim os eletrodos. Em alguns projetos, ao invés de vaporização, o metal pode ser depositado em forma de pasta.
CURIOSIDADE: O mesmo acontece nos capacitores de Mica, em que a Prata precisa ser vaporizada na superfície do dielétrico, pois ele não é perfeitamente 'liso', ou seja, não existiria um contato elétrico perfeito caso simplesmente fosse colocado um filme metálico como armadura pra estes capacitores.
Para saber mais sobre os capacitores de Mica, CLIQUE AQUI!
A vaporização de metal permite sua impregnação na superfície áspera do dielétrico da mesma forma como ocorre com o feltro embebido em líquido condutor nos capacitores eletrolíticos de Óxido de Alumínio.
Para saber mais sobre os capacitores eletrolíticos de Óxido de Alumínio, CLIQUE AQUI!
Os eletrodos
Um problema particular na produção de capacitores de chip de cerâmica multicamadas no final da década de 1990 foi um forte aumento no preço dos metais usados para eletrodos e terminais.
As escolhas pioneiras foram os metais nobres não oxidáveis Prata e Paládio, que podem suportar altas temperaturas de sinterização de 1200 a 1400 °C. Eles eram chamados de "NME" (Noble Metal Electrode, em português "Eletrodo de Metal Nobre") e ofereciam propriedades elétricas muito boas para capacitores de Classe 2. O aumento do preço desses metais elevou muito os preços dos capacitores.
O custo levou ao desenvolvimento do BME (Base Metal Electrodes) usando materiais muito mais baratos e comuns, no caso, Níquel e Cobre.

Imagem 2 - As camadas "Inner", "Middle" e "Outer" compõem o terminal do componente SMD
Entretanto, a metalização BME produziu propriedades elétricas diferentes. Por exemplo, o 'desalinhamento' entre tensão e capacitância nos X7R aumentou significativamente, bem como o fator de perda e o comportamento da impedância dos capacitores de cerâmica de Classe 2 como um todo foram 'piorados' pela metalização BME. Todavia, pelas características que possuem (também por razão do custo), essas variações negativas foram finalmente aceitas pelo mercado, enquanto a metalização NME foi mantida nos capacitores de cerâmica Classe 1.
Nesta parte do texto são apresentados detalhes sobre o comportamento do capacitor de cerâmica quando em operação num circuito. Isto está diretamente relacionado com sua classificação.
Capacitância x Temperatura
A capacitância dos cerâmicos varia com a temperatura. Os diferentes dielétricos dos muitos tipos de capacitores mostram grandes diferenças na dependência da temperatura.
O coeficiente de temperatura é expresso em partes por milhão (ppm) por grau Celsius para capacitores de cerâmica de Classe 1 ou em porcentagem (%) sobre a faixa total de temperatura para capacitores de Classe 2.

Tabela 5 - Coeficientes de temperatura de alguns capacitores cerâmicos
Capacitância x Frequência
A maioria dos tipos cerâmicos tem mudanças de capacitância maiores ou menores com o aumento da frequência. A rigidez dielétrica da película de cerâmica ou plástico Classe 2 diminui com o aumento da frequência, ou seja, seu valor de capacitância diminui. Este fenômeno está relacionado à relaxação dielétrica em que a constante de tempo dos dipolos elétricos é a razão para a dependência da permissividade com a frequência. O gráfico abaixo mostra o comportamento típico da frequência para capacitores Classe 2 em comparação com os Classe 1.

Gráfico 1 - A capacitância em relação à frequência aplicada para capacitores de cerâmica X7R e Y5V de Classe 2 (curva de NP0 da Classe 1 para comparação)
Capacitância x Tensão
A capacitância dos cerâmicos também pode mudar com a tensão aplicada. Este efeito é mais comum em capacitores de Classe 2. O material ferroelétrico depende da tensão aplicada. Quanto maior a tensão elétrica aplicada, menor a permissividade.
A capacitância medida / aplicada com tensão mais alta pode cair para valores de -80% do valor medido com a tensão de medição padronizada de 0,5 ou 1,0 V.
Dependência da tensão da capacitância para alguns capacitores de cerâmica de classe 2 diferentes:
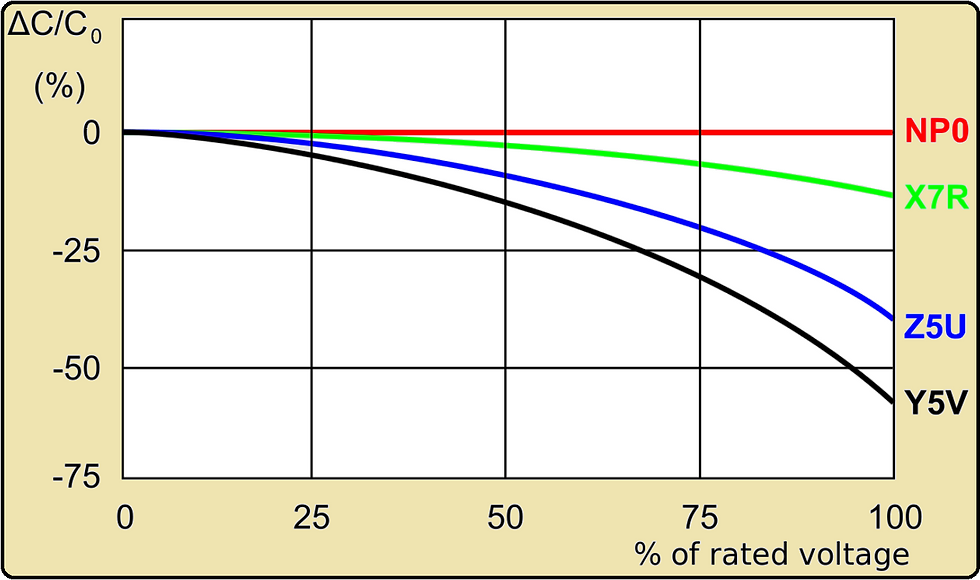
Gráfico 2 - De maneira simplificada, a mudança na capacitância em função da tensão aplicada para capacitores de 25 V em diferentes tipos de graus de cerâmica
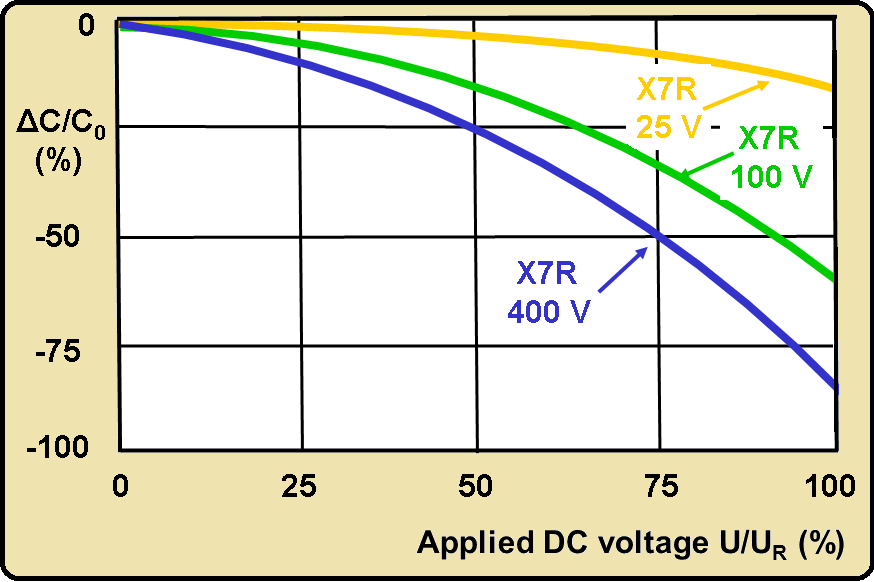
Gráfico 3 - De forma simplificada, a mudança na capacitância em função da tensão aplicada para cerâmicas X7R com diferentes tensões nominais
Este comportamento é uma pequena fonte de não linearidade em filtros de baixa distorção e outras aplicações analógicas. Em aplicações de áudio, esse pode ser o motivo das distorções harmônicas.
OBSERVAÇÃO: Note que os gráficos até aqui levam mais em conta a oscilação de temperatura do que a capacitância em si. Lembre-se agora dos termistores PTC, que fazem uso de cerâmicas que também mudam suas propriedades elétricas de acordo com a temperatura. Para saber mais sobre os termistores, CLIQUE AQUI!
À prova de tensão
Para a maioria dos capacitores, uma rigidez dielétrica fisicamente condicionada ou uma tensão de ruptura geralmente pode ser especificada para cada material dielétrico de acordo com suas dimensões. Isso não é possível com capacitores de cerâmica.
A tensão de ruptura de uma camada dielétrica de cerâmica pode variar dependendo do material do eletrodo e das condições de sinterização da cerâmica até um fator de 10. Um alto grau de precisão e controle dos parâmetros do processo é necessário para manter a dispersão das propriedades elétricas das camadas cerâmicas muito finas dentro dos limites especificados.
A prova de tensão dos capacitores de cerâmica é especificada como tensão nominal (UR). Esta é a tensão contínua máxima que pode ser aplicada ao capacitor até o limite superior de temperatura. Esta prova de tensão garantida é testada de acordo com as tensões mostradas na tabela ao lado.
Além disso, em testes periódicos de tempo de vida (testes de resistência), a prova de tensão dos capacitores de cerâmica é feita com um valor ainda maior (120 a 150% de UR) para garantir uma construção segura.

Tabela 6 - Note a coluna com os valores de tensão nominal e a coluna com os valores para testes de tempo de vida
Os valores da tabela acima estão relacionados ao IEC 60384-8 / 21/9/22.
Envelhecimento
Em capacitores de cerâmica de Classe 2, a capacitância diminui com o tempo. Este comportamento é denominado "envelhecimento". O envelhecimento ocorre em dielétricos ferroelétricos, onde os domínios de polarização espontânea no dielétrico contribuem para a polarização total.
A degradação dos domínios polarizados no dielétrico diminui a permissividade ao longo do tempo, de modo que a capacitância dos cerâmicos de Classe 2 diminui à medida que o componente envelhece.
O envelhecimento segue uma lei logarítmica. Esta lei define a diminuição da capacitância como uma porcentagem por uma década de tempo após o período de recuperação da soldagem em uma temperatura definida. Por exemplo, no período de 1 a 10 horas a 20 ° C. Como a lei é logarítmica, a perda percentual de capacitância será duas vezes entre 1 he 100 he 3 vezes entre 1 he 1000 he assim por diante. Portanto, o envelhecimento é mais rápido perto do início e o valor da capacitância se estabiliza efetivamente com o tempo.
A taxa de envelhecimento dos capacitores de Classe 2 depende principalmente dos materiais usados. Como regra geral, quanto maior for a dependência da cerâmica com a temperatura, maior será a porcentagem de envelhecimento. O envelhecimento típico dos capacitores cerâmicos X7R é de cerca de 2,5% por década. A taxa de envelhecimento dos capacitores cerâmicos Z5U é significativamente maior e pode chegar aos 7% por década.
CURIOSIDADE: O processo de envelhecimento dos capacitores classe 2 pode ser revertido aquecendo o componente acima do ponto Curie.
Capacitores de Classe 1 não sofrem envelhecimento como os de Classe 2. Mas as influências ambientais, como temperatura mais alta, umidade elevada e estresse mecânico podem, por um longo período de tempo, levar a um pequeno declínio irreversível na capacitância, às vezes também chamado de envelhecimento. A variação da capacitância para P 100 e N 470 Classe 1 é menor que 1%, para capacitores com cerâmica N 750 a N 1500 é ≤ 2%.
CURIOSIDADE: Os capacitores de cerâmica podem sofrer alterações em seus parâmetros elétricos devido ao estresse de soldagem. O calor do banho de solda, especialmente para estilos SMD, pode causar mudanças na resistência de contato entre os terminais e os eletrodos.
Para capacitores de cerâmica ferroelétricos Classe 2, a temperatura de soldagem está acima do ponto de Curie. Ao passar desta temperatura, a fase paraelétrica predomina, todavia, os domínios polarizados no dielétrico voltam após a soldagem e o processo de envelhecimento dos capacitores de cerâmica Classe 2 começa novamente.
Com isso, depois de soldar é necessário um tempo de recuperação de aproximadamente 24 horas. Após a recuperação, alguns parâmetros elétricos como por exemplo o valor de capacitância, ESR e correntes de fuga são alterados irreversivelmente. As mudanças são pequenas e dependem das especs. gerais do capacitor.

Aqui são apresentados os tipos mais comuns e até os obsoletos formatos de capacitores cerâmicos.

Imagem 3
CURIOSIDADE: O capacitor cerâmico de cor azul na imagem acima é muito utilizado em aparelhos eletrônicos para filtrar transientes oriundos da rede elétrica. Estes modelos possuem características mais robustas (tensão e capacitância). Existem duas formas de aplicação: a "X" e a "Y". Ambas serão explicadas em artigos futuros!
Capacitor cerâmico Radial (disco) PTH
Abaixo, você vê o diagrama simplificado de um capacitor de cerâmica em formato de disco radial:

Diagrama 1
Como pode se ver na imagem, há apenas um disco de cerâmica entre dois eletrodos (armaduras). Este disco é dimensionado para ter uma determinada rigidez dielétrica para que o capacitor consiga suportar uma determinada carga e uma determinada tensão de trabalho.
O tamanho (área e espessura) dos dielétricos obviamente devem ser levados em conta, afinal, até que não ocorra a polarização dielétrica, a carga ficará contida nas armaduras (eletrodos).
Há também um invólucro de material isolante elétrico, normalmente resina de Poliepóxido, que cobre o núcleo do componente, protegendo de sujeira, umidade e impactos. Após o 'miolo' com os eletrodos e os dois terminais estarem prontos, o componente é mergulhado no poliepóxido não curado.
CURIOSIDADE: Para saber mais sobre a formulação do Poliepóxido e seu processo de cura, bem como algumas características desse material plástico, comece CLICANDO AQUI!
Os dois pinos, ou melhor dizendo, os terminais, são soldados nos eletrodos. Após isso, é feita uma limpeza pra desengordurar, tirar a contaminação para que então possa ser aplicada a camada de resina para isolar e reforçar o componente.
Capacitor de Camada de Barreira
A estrutura do capacitor de camada de barreira interna (IBLC - Internal Barrier Layer Capacitor) é apresentada abaixo:

Diagrama 2 - Como é estruturada a cerâmica semicondutora utilizada nestes capacitores
Tais capacitores possuem grãos cerâmicos maiores e tendem a ter tamanho mais avantajado que os outros capacitores cerâmicos. Eles pertencem à Classe 3, possuem invólucro feito da mesma forma e com mesma resina dos capacitores cerâmicos 'disco'.
Capacitor cerâmico SMD
Já os capacitores de cerâmica SMD (Surface Mounting Devices - Dispositivo de Montagem em Superfície) se baseiam em várias 'folhas' de cerâmica intercaladas com eletrodos metálicos. Abaixo, capacitores cerâmicos em formato SMD:
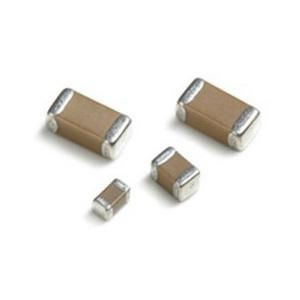
Imagem 4
Para reduzir a ESR, os fabricantes utilizam de uma concepção multicamadas (multilayer). Estes capacitores são uma espécie de "sanduíche" de camadas de cerâmica intercaladas com eletrodos, além do mais, vários materiais são empregados. Pela lógica, é como se vários capacitores iguais em paralelo fossem colocados dentro de um único componente. Observe o próximo diagrama:
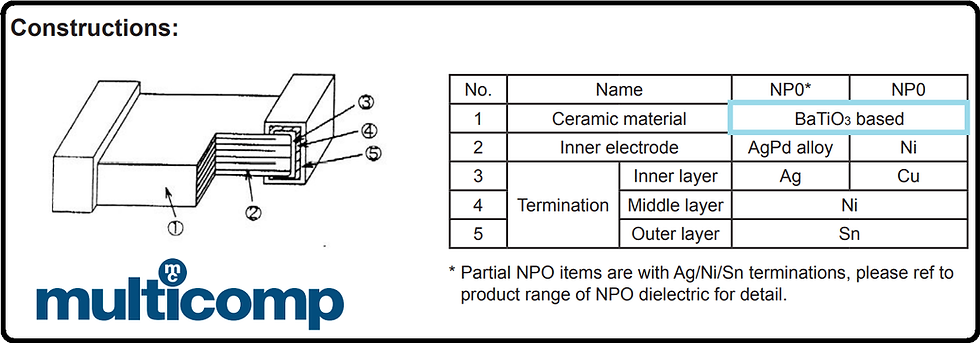
Diagrama 3 - Note a quantidade de elementos químicos empregados
Essa construção ultra compacta de várias camadas de dielétrico intercaladas com armaduras também pode ser vista em capacitores poliméricos de Óxido de Tântalo (componentes SMD também conhecidos como POSCAP). Eles utilizam uma tecnologia chamada "multi-ânodo". Para saber mais sobre isso, CLIQUE AQUI!
Veja o próximo diagrama:

Diagrama 4 - A estrutura dos capacitores cerâmicos SMD
Estes capacitores apresentam baixas perdas, alta resistência de isolação, capacitância estável e alta capacitância em pequenas dimensões.
Também conhecidos como "capacitores MLCC" (Multilayer Ceramic Chip Capacitor), os cerâmicos SMD são baratos de se produzir e trabalham melhor com altas frequências, no entanto, possuem um baixo desempenho térmico, uma estrutura física frágil (racham facilmente) e são mais suscetíveis a efeitos piezoelétricos. Apesar dos contras, é fácil encontrar blocos destes componentes em circuitos de alimentação de placas de vídeo, por exemplo.
CURIOSIDADE: Placas de vídeo também podem combinar capacitores MLCC com blocos de capacitores POSCAP (Conductive Polymer Tantalum Solid Capacitors) ou apenas capacitores POSCAP. Os POSCAPs não lidam bem com altas frequências, são bem maiores, porém aguentam altas temperaturas, demoram mais pra se degradar e não sofrem com efeitos piezoelétricos.
Quanto as rachaduras, a indústria também estudou formas de fazer com que pequenas trincas não prejudicassem o capacitor como um todo.
A cerâmica é um sólido muito duro, tão rígido ao ponto de ser frágil.
Os SMDs MLCC são suscetíveis a tensões de flexão, uma vez que são montados diretamente no substrato. Presos por pontos de solda na placa de circuito impresso (PCB), eles são frequentemente expostos a tensões mecânicas, como por exemplo a vibração. Cerâmicos também são mais sensíveis a tensões térmicas.
O tamanho e formato do ponto de solda pode multiplicar essas tensões e causar rachaduras nos cantos do capacitor:
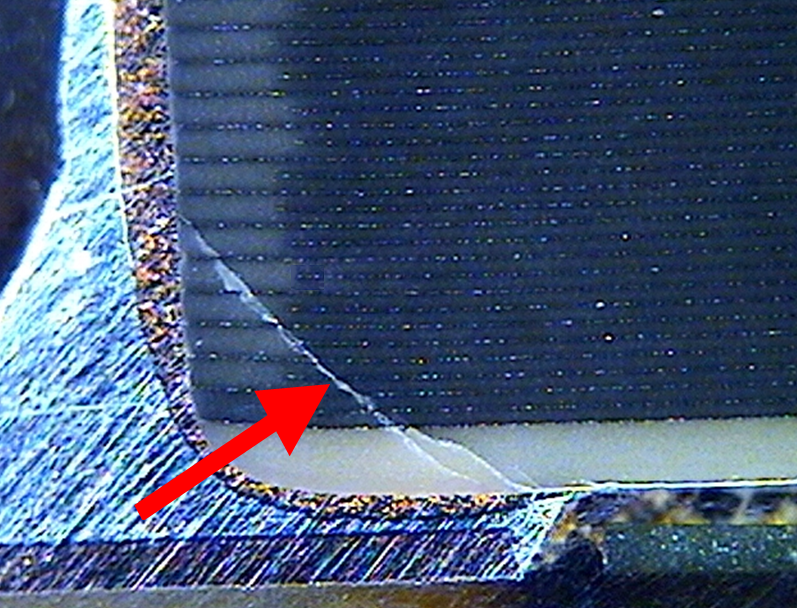
Imagem 5 - Rachadura no canto de um cerâmico em formato SMD
De todos os fatores de influência, causar um choque mecânico no PCB provou ser o mais crítico. A razão é que as forças induzidas por esses tipos de tensões são mais transmitidas com pouco amortecimento para os componentes via juntas de solda.
Com recursos de projeto avançados, particularmente pelo design dos eletrodos e terminações, a resistência à flexão pode ser melhorada. Por exemplo, um curto-circuito interno surge pelo contato de dois eletrodos com polaridades opostas, que serão produzidos por uma trinca na região onde os eletrodos são ligados nos terminais. Isso pode ser evitado quando as superfícies de sobreposição dos eletrodos são reduzidas. Isso é obtido, por exemplo, por um "Design de modo aberto" (OMD). Aqui uma quebra na região das terminações só reduz um pouco o valor da capacitância.
Na tabela abaixo, alguns tipos de construção de capacitores de cerâmica SMD MLCC:
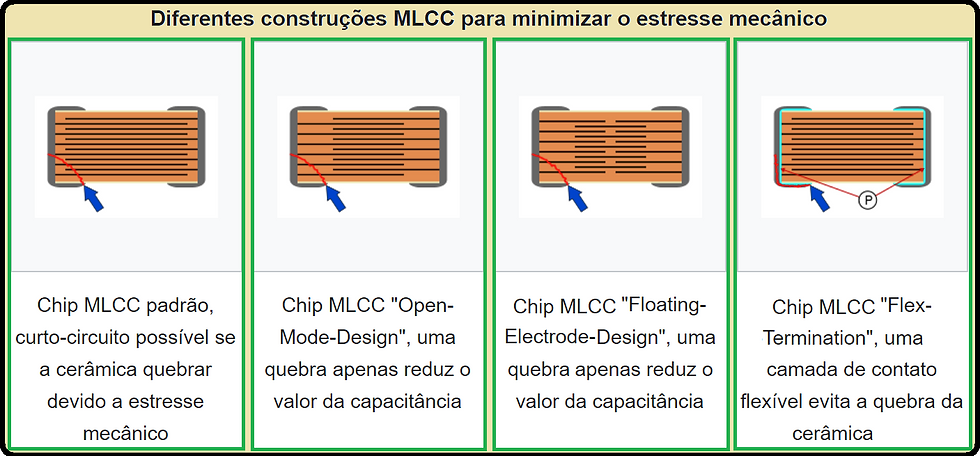
Tabela 7 - As arquiteturas de chips MLCC para reduzir problemas com trincas
Com uma construção semelhante chamada "Floating Electrode Design" (FED) ou "Multi-layer Serial Capacitors" (MLSC), também, somente a redução da capacitância resulta se partes do corpo do capacitor quebrarem. Esta construção funciona com um conjunto extra de eletrodos flutuantes (sem nenhuma conexão condutiva aos terminais). Uma quebra não leva ao curto-circuito, apenas à redução da capacitância. No entanto, ambas as estruturas resultam em componentes maiores em relação a uma versão padrão do MLCC com o mesmo valor de capacitância.
O mesmo volume em relação aos MLCCs padrão é obtido pela introdução de uma camada intermediária flexível de um polímero semicondutor entre os eletrodos e a terminação chamada de "Flex-Termination" (FT-Cap), ou "Terminais Soft". Nesta construção, os terminais metálicos podem mover-se contra a camada de polímero flexível e, portanto, absorver forças de flexão, sem resultar em quebra da cerâmica.
CURIOSIDADE: Para saber mais sobre semicondutores orgânicos e inorgânicos, CLIQUE AQUI!
Para finalizar o tópico "capacitores SMD", um último diagrama:

Diagrama 5 - Note o uso massivo do Titanato de Bário
CURIOSIDADE: Com a miniaturização progressiva da eletrônica digital nas últimas décadas, os componentes na periferia dos circuitos lógicos integrados também foram reduzidos. O aprimoramento de um MLCC envolve a redução da espessura dielétrica e o aumento do número de camadas. Ambas as opções exigem grandes esforços e estão conectadas com muita experiência.
Em 1995, a espessura mínima do dielétrico era de 4 µm. Em 2005, alguns fabricantes produziram chips MLCC com espessuras de camada de 1 µm. A partir de 2010, a espessura mínima é de cerca de 0,5 µm. A intensidade do campo no dielétrico também aumentou para 35 V / µm.
A redução do tamanho desses capacitores é conseguida reduzindo o tamanho do grão do pó, afinando as camadas de cerâmica. Além disso, o processo de fabricação aprimorou-se e possui cada vez mais precisão, de modo que mais e mais camadas podem ser empilhadas.
Entre 1995 e 2005, a capacitância de um capacitor Y5V MLCC de tamanho 1206 foi aumentada de 4,7 μF para 100 μF. Já em 2013, muitos produtores podiam fornecer capacitores MLCC Classe 2 com um valor de capacitância de 100 μF no tamanho 0805.
Para saber mais sobre a padronização dos formatos SMD, CLIQUE AQUI!
Capacitor cerâmico tubular PTH
Há também os capacitores tubulares, isto é, que utilizam um tubo de cerâmica e com a vaporização de material metálico em suas bordas, onde é soldado os terminais. Eles foram muito comuns entre a década de 1950 e 1970.
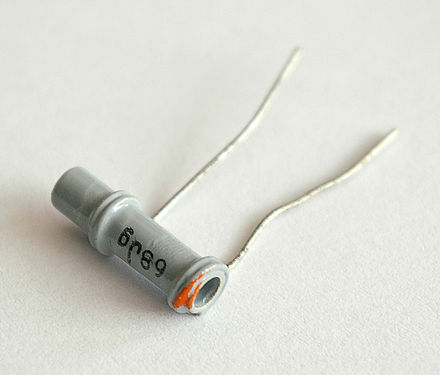
Imagem 6 - Capacitor cerâmico em formato axial tubular
Capacitor cerâmico Plate PTH
Outro modelo de capacitor das antigas, que já não é fácil de se encontrar nas lojas, apenas em equipamentos jurássicos é o capacitor "plate". Ao invés de um disco de cerâmica, eles utilizam um dielétrico em formato de 'chapa' retangular.
Esses componentes eram aplicados em circuitos UHF e VHF, principalmente, e também há modelos com capacitância na casa dos nanoFarads. Veja abaixo uma imagem de capacitores plate:

Imagem 7
Na comunidade eletrônica há alguns que elogiam e outros que reclamam dos capacitores plate. Em lugares muito úmidos eles se deterioravam com facilidade, mas ao mesmo tempo apresentavam baixa tolerância, eram bem pequenos e estáveis. O sistema de identificação destes capacitores era por uma tabela de cores, que é apresentada logo abaixo, na sequência deste texto.

Como fazemos para saber quantos Pico Farads ou nano Farads possui um determinado capacitor cerâmico? Aí temos um problema! Vários modelos informam a capacitância na carcaça, outros apenas um código que deve ser traduzido e outros não informam nada!
Os capacitores que não possuem nenhuma inscrição, na maioria das vezes são os SMD que, por serem muito pequenos, não sobra espaço no invólucro para informar seus especificações, desta forma, apenas tendo o diagrama do circuito e sendo um bom técnico para descobrir!
Capacitores cerâmicos de tamanhos comuns, apresentam um código com alguns números e até uma ou duas letras. Veja a tabela abaixo:
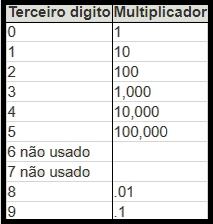
Tabela 8
É uma tabela de multiplicadores, similar a utilizada em resistores: Os primeiros dois dígitos devem ser concatenados com a quantidade de zeros que o último representa.
EXEMPLOS:

Devemos concatenar o valor 20 com 0, já que o número 1 representa a adição de um zero. Desta forma temos 200 pF (Pico Farads).
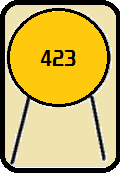
Da mesma forma que aconteceu no primeiro exemplo, o "3" vale três zeros, portanto, temos o valor 42 + 000 que é igual a 42.000 pF ou simplesmente 42 nF (Nano Farads).
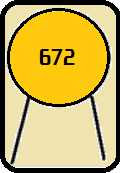
O número 2 vale "00", portanto, temos 67 + 00 que é igual a 6700 pF ou simplesmente 6,7 pF. Quando aparecer valores com a letra "k" no meio, por exemplo, 4k7, 2k3, significa a mesma coisa: para 4k7 temos 4700 pF e para 2k3 temos 2300 pF.
Quando aparecer a letra "n" também devemos leva-la em consideração. Por exemplo, os valores 2n2 e 4n3 significam 2,2 nF (2200 pF) e 44.300 nF (44,3 pF), respectivamente.
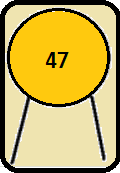
Há apenas dois dígitos, e agora? Este capacitor vale 47 pF.
Quando aparecer valores com a letra 0 no final, como por exemplo, 100, 500, devemos ignorá-lo. Assim, para 100 temos 10 pF e para 500 temos 50 pF.
Alguns modelos de capacitores apresentam seu valor exato na carcaça, portanto para saber e utilizam o sistema de codificação explicado acima ou se apresentam o valor real na carcaça, só vendo no diagrama do circuito em questão!
Por exemplo, podemos encontrar capacitores de cerâmica com valor 452 e ele realmente ser de 452 pF. Podemos achar capacitores com o valor 200 e ele ter 200pF.
Outros capacitores possuem a mesma forma de identificação mostrada nos exemplos acima, mas uma letra após o número, que identifica a tolerância do capacitor, além de uma listra no topo do componente que identifica o coeficiente de temperatura.
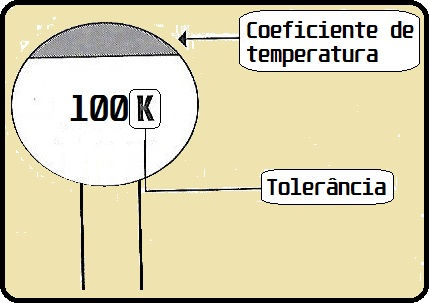
Imagem 8
Esse sistema é o norte-americano. A tabela com a tolerância que cada letra representa é mostrada abaixo:

Tabela 9
Note que, mais abaixo mostramos o sistema de identificação para alguns capacitores SMD e eles utilizam a mesma tabela de letras.
Para capacitores cerâmicos com sistema de identificação europeu, segue a lista:

Tabela 10
Um sistema de identificação de capacitância muito antigo e já abandonado, é o de código de cores. Ele funciona da mesma forma que os resistores. São 3 listras, sendo que, o primeiro e o segundo valor devem ser concatenados e multiplicados pelo terceiro. Alguns capacitores apresentam apenas duas listras, mas isso é devido a idade dos componentes que, com o tempo, a cor marrom da listra vai se desbotando e ficando imperceptível.
Não há um padrão principal de nomenclatura. Alguns poucos capacitores cerâmicos SMD podem ter os mesmos sistemas de identificação descritos neste texto, mas mesmo assim você pode confundi-los com resistores SMD, pois estes componentes em formato miniatura são, em muitos casos, completamente idênticos.
Abaixo, uma tabela com um sistema de nomenclatura utilizado em alguns capacitores cerâmicos SMD:
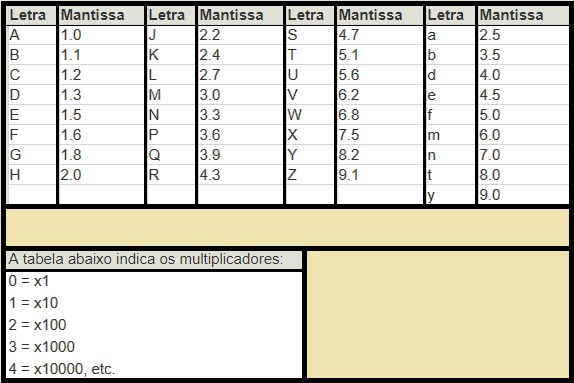
Tabela 11
Por exemplo, um capacitor cerâmico SMD com a inscrição "A1" significa que ele possui 100 pF.
Mas calma que não é só isso! Temos que ver os valores de tolerância destes capacitores. Normalmente, além dos números, há uma letra. Observe a tabela abaixo:

Tabela 12
Por exemplo, um capacitor cerâmico com o valor 47H significa que ele possui 47 pF e uma tolerância de +/- 3 %.
Para os capacitores plate, uma tabela de cores era utilizada, e ela é apresentada abaixo:
Tabela 13
A tolerância destes capacitores e outras características devem ser procuradas no datasheet.

Neste tópico, trago alguns detalhes extras sobre tudo o que já foi explicado.
Substituindo os de Tântalo
Os capacitores de cerâmica MLCC são cada vez mais usados para substituir os capacitores eletrolíticos de Óxido de Tântalo e Óxido de alumínio de baixa capacitância em aplicações como bypass ou fontes de alimentação comutadas de alta frequência, à medida que seu custo, confiabilidade e tamanho se tornam competitivos. Em muitas aplicações, seu baixo ESR permite o uso de um valor de capacitância nominal inferior.
Microfonia
Todos os cerâmicos de Classe 2 usando cerâmica ferroelétrica exibem piezoeletricidade, apresentando um efeito chamado microfonia.
A microfonia descreve o fenômeno em que componentes eletrônicos transformam vibrações mecânicas em um sinal elétrico que, em muitos casos, gera um ruído indesejado. Pré-amplificadores eletrônicos sensíveis geralmente usam cerâmica Classe 1 e capacitores de filme plástico para evitar este efeito.
No efeito microfônico reverso, o campo elétrico variável entre as placas do capacitor exerce uma força física, movendo-as como um alto-falante. Cargas de impulso de alta corrente ou altas correntes de ondulação podem gerar som acústico audível vindo do capacitor, mas sobrecarregando o dielétrico.
Para saber mais sobre o 'coil whine' e o 'caps whine', CLIQUE AQUI!
O processo de fabricação dos cerâmicos MLCC

Diagrama 6 - A produção dos capacitores cerâmicos MLCC
O material de partida para todos os chips MLCC é uma mistura de grânulos finamente moídos de matérias-primas paraelétricas ou ferroelétricas, modificados por aditivos determinados com precisão. Esses materiais em pó são misturados homogeneamente. A composição da mistura e o tamanho das partículas do pó são tão pequenas quanto 10 nm.
Uma fina folha destes materiais é criada a partir de uma suspensão do pó com um aglutinante adequado. Esta fina folha é cortada em vários pedaços iguais, que são serigrafadas com uma pasta de metal, formando os eletrodos. Em um processo automatizado, essas folhas são empilhadas no número necessário de camadas e solidificadas por pressão. Além da permissividade relativa, o tamanho e o número de camadas determinam o valor de capacitância posterior.
A pilha em camadas é pressionada e cortada em componentes individuais. É necessária alta precisão mecânica, por exemplo, para produzir uma pilha de 500 ou mais camadas de tamanho "0201" (0,5 mm × 0,3 mm).
Após o corte, é feito a sinterização de todos estes pequenos capacitores. Isso ocorre em temperaturas entre 1.200 e 1.450 ° C, produzindo a cerâmica. Este processo de queima cria as propriedades dielétricas desejadas.
A queima é seguida pela limpeza e confecção dos terminais elétricos. Através da metalização, as pontas dos eletrodos internos são conectados em paralelo e o capacitor recebe seus terminais. Por fim, será feita uma medição de 100% dos valores elétricos e a criação dos bobinados que serão desenrolados pelos robôs que fazem a montagem dos componentes nas placas de circuito.

Vamos resumir todo o texto em alguns pontos:
→ Os capacitores de cerâmica ganharam mercado pelo motivo de não haver tanta disponibilidade dos dielétricos de Mica no mercado (escassez de matéria prima) e por terem características semelhantes;
→ Capacitores cerâmicos Classe 1 são paraelétricos, isto é, não possuem domínios com polarização espontânea, e também não envelhecem;
→ Capacitores cerâmicos Classe 2 são ferroelétricos, isto é, possuem domínios com polarização espontânea e envelhecem;
→ Acima do ponto de Curie, a fase paraelétrica predomina.
Abaixo do ponto de Curie, a fase ferroelétrica predomina.
O composto cerâmico dos capacitores de Classe 1 está na fase paraelétrica em toda a faixa de temperatura de operação, ao contrário dos de Classe 2;
→ A variação de capacitância é em decorrência das características do dielétrico, que mudam de acordo com a temperatura e a frequência aplicada
Para capacitores de Classe 1, essa variação é mínima, então consideram-os 'lineares'.
Para capacitores de Classe 2, essa variação pode ser grande, então consideram-os não lineares.

Existem outros sistemas de nomenclatura menos utilizados para capacitores cerâmicos. Como você pode ver, sempre haverá confusão na hora de identificar um capacitor cerâmico!
Se você gostou do artigo é só curtir e compartilhar! Caso tenha ficado com alguma dúvida, mande um e-mail para hardwarecentrallr@gmail.com.
FONTES e CRÉDITOS
Textos, imagens e tabelas: Leonardo Ritter; Google imagens.
Fontes: Instituto Newton C. Braga; Grupo Alternativo de Carga Pesada (site); StringFixer; Wikipedia (somente artigos com fontes verificadas!); Eletrônica Aqui; Livro "Eletrônica Para Autodidatas, Estudantes e Técnicos" do Gabriel Torres.
Ultima atualização: 02 de Setembro de 2022.